Hvordan man opbygger en skumbåd video. Skumbåd
Problemet med en lille fiskerbåd blev bestemt uventet. Jeg havde en skumplast, der tidligere fungerede som en vægbeklædning til et gammelt hus. At være bekendt med teknologien om at bygge en skumbåd ved at kende processen med at klæde skroget med glasfiber, kiggede jeg stadig på "Både og Yachter" og til min overraskelse fandt jeg, at beskrivelsen af en sådan båd først blev fundet i 1975. Jeg betragter den manglende opmærksomhed på sådanne både ufortjent, da den har en række ubestridelige fordele som skumplast. I båden er det varmt, det krøller ikke, hvilket er vigtigt, når man fisker, har en lav vægt og en stor reserve af opdrift. Byggeprocessen er enkel og tager lidt tid.
Grundlæggende båddata
Båden "Gamma", bygget af Yu. Nikiforov, passede mig ikke på grund af designets kompleksitet. For en sådan båd er det nok at have enklere konturer, med en flad, uden at løfte op, bunden og tarmsnuden. Erklæringen fra Yu. Nikiforov vedrørende udnyttelsen af den "barske" skumkrop uden glasfiberpasta var også i tvivl. Baseret på disse overvejelser byggede jeg en båd ved hjælp af følgende teknologi om få dage fra PVC-skummet. Først skære og kørte tre store plader skum. Af dem sidder bunden. Ved hjælp af støtten, svarende til rack-keelblock "Gamma", blev den endelige samling af skroget. De 40 mm tykke skumplader blev forbundet med hinanden med epoxylim baseret på ED-5 harpiks.
Polystyren PVC kan erstattes af en anden kvalitet PS-1 eller PSBS. De skar også godt med en skarp kniv og savet med en hacksav. Yu. Nikiforov skåret skumplastik nichrome streng, opvarmet ved at forbinde det og elnettet. Det skal dog være opmærksom på, at PS-skum, der indeholder styren, er opløst af polyesterharpikser, derfor er det muligt at limme kropsdele eller lim det kun med glasfiber på et epoxybaseret bindemiddel.
Kroppen uden glasfiberindpakning vejer 20 kg, men driften af en sådan båd vil kræve stor omhu, da skum vil slides hurtigt ud, og selv et strejf af en tændt cigaret kan ødelægge dit barn. For at give kroppen større stivhed og styrke, skal du i dette tilfælde lægge et par dåser, der brister i siden. Langs omkredsen af sagen er det nødvendigt at fastgøre en eg bar - flange på lim og skruer. Ikke overflødig og to strimler på bunden, som vil beskytte den mod slid, når du trækker båden til kysten. Det er også nødvendigt at beskytte stødsammenføjningerne uden for sagen og indsætte dem f.eks. Med strimler af klud.
Vi besluttede at indsætte over sagen udenfor med glasfiber. Skrogets vægt steg lidt, men bådens holdbarhed steg.
I stedet for en krukke bruger jeg en lille højde skumplade: sidder på den, jeg er beskyttet af siderne fra vinden. Båden går godt under årerne og sniger sig let ind i vassen, takket være en ret skarp næsekontur.
Ører ca. 2 m lange med flade blade 350X150 mm - kajak type. For at kunne bruge påhængsmotoren skal tromlen forstærkes, som vist i diagrammet.
Normalt vurderer amatørskibsbyggere, når de møder med noget nyt materiale, først og fremmest udgangspunktet for anvendelighed til bygning af en båd. Polyfoam var ingen undtagelse. Det begyndte straks at blive anvendt som isolering for at sikre oversvømmelighed, når der bygges glasfiberkar - til fremstilling af monteringsenheder. Men af en eller anden grund er skum ikke brugt som det vigtigste strukturelle materiale, selv om småbåde, penduler og slæbebåde efter min mening kan og bør gøres af det.
instruktion
Egenskaber af skum og udvidet polystyren
Høj varmeisolering. Med hensyn til varmebevægelse overgår skumplastik de fleste isoleringsmaterialer.
Ease. Med al dens effektivitet vejer skumplast overraskende lidt, da 98% af sin masse er luft. Hvis du sammenligner det ekspanderede polystyren på denne egenskab med andre isoleringsmaterialer, opnås følgende andel:
Skumpladen 50 mm tykk er:
. 100 mm mineraluld
. eller 200 mm træ
. eller 325 mm ekspanderet ler;
. eller 900 mm mursten;
. eller 1400 mm beton.
Herfra viser det sig, at skumens isolering, idet der tages hensyn til installationsarbejdet, koster 20-50 gange mindre end isoleringen af andre materialer. Og brugen vil spare nogle flere penge på opvarmning!
Skum egenskaber
Miljøvenlighed. Helt sikkert, derfor bruges den også i fødevareindustrien. Styrofoam forhindrer dannelsen af bakterier og skimmel. Den kan frit benyttes ved temperaturer: fra - 60 til + 80 grader.
Sikkerhed. Det er kendt, at skummet under forbrændingen vil udstyre de samme elementer som det brændende træ. Og de seneste forbedringer gør det muligt for os at give skummet modstand mod ild. Stoffet der er indeholdt i skumplastik brandhæmmende forhindrer forbrænding og fremmer selvslukning. Henviser til gruppen af brandbarhed G4.
Vandtæt. Skummet i løbet af året absorberer fra 1,5 til 3,5% fugt. Det taler om dets høje fugtighedsbestandighed. Det er værd at bemærke, at der er et direkte forhold mellem skumets åndbarhed og fugtighedsbestandighed. Den første funktion forbedrer den anden. Denne ejendom tillader boliger at "trække vejret".
Styrke. Under påvirkning af mekaniske belastninger i skumplastik - polystyrenskum, observeres en viskoelastisk reaktion, som sikrer sin høj styrke. Dens trykstyrke er mindst 0,04-0,20 MPa. Samtidig bevarer materialet sin oprindelige størrelse og ændrer ikke placeringen.
Lydisolering. Skumfinishen giver mulighed for at øge beskyttelsen mod ekstern støj med 2-4 dB.
udstyr
Polyfoam-fremstillingsteknologi
Skumgrundlaget er polystyren - en termoplastisk polymer. På grund af dens vandmodstand er evnen til at tage enhver form under påvirkning af temperatur, frostresistens, polystyren i vid udstrækning brugt i industrien (brugstilstand: skabe en beholder til yoghurt). Imidlertid er polystyren stadig nepoplast.
Den fremstilles ved skumdannelse af polystyrengranuler. Efter opskumning behandles de med opvarmet vanddamp, hvorefter hele proceduren gentages.
Cycliske skummeprocesser kan signifikant reducere tætheden af polystyrengranuler, hvilket fører til et fald i deres vægt. Efter sekundær skumning skal skummet tørres. Tørring er fjernelse af resterende fugt fra overfladen af polystyrenskum (vand går ikke indvendigt - det skum-vandtætte materiale).
Tørring foregår udendørs - det er på dette stadium, at luften fylder porerne i materialet og erhverver en komplet form. Størrelsen af granulaterne kan variere fra 5 til 15 millimeter.
Tørret udvidet polystyren har brug for støbning. Det forarbejdede materiale presses ved hjælp af specielle maskiner og underkastes tertiær behandling med varm damp. Som et resultat af støbning ser det ud som en blok af hvid farve af en vis tykkelse. Blokken er skåret i de krævede formularer og i denne form sendes til kunden.
Vigtigt: Skummet kan skæres ikke kun i overensstemmelse med typiske parametre, men også i overensstemmelse med de enkelte dimensioner, der kræves til en bestemt konstruktion.
Styrofoamskæring udføres på maskiner med vandret og lodret form for opskæring. Ved skæring af dens struktur er ikke beskadiget, er støbning hurtig. Den eneste teknologiske tilstand: Temperaturen i værkstedet, hvor skæring er færdig, bør ikke falde under 18ºС, ellers vil skummet bryde (smuldre).
Et andet træk ved produktionen: selve teknologien og råmaterialerne er relativt billige, hvilket kan reducere omkostningerne ved slutproduktet betydeligt. Det er sikkert at sige, at skummet ikke kun er en sikker og pålidelig isolering, det er også en af de billigste.
Den lave pris på materialet kombineret med dens funktionalitet gør det særligt populært inden for anlægsarbejder.
Gør det selv
Holdbarhed og holdbarhed af polyfoam
Skummet har ikke en høj densitet (50 gange lavere end vandets), men det viser alligevel fremragende modstand over for ensartede mekaniske belastninger, både i spænding og i kompression.
Polyfoam er i stand til at modstå tryk i årevis uden at blive deformeret uden at kollapse og uden at ændre dens fysiske egenskaber. En levende illustration kan være dens udbredt anvendelse i opførelsen af landingsbaner. Styrkeindekset afhænger i høj grad af tykkelsen af polystyrenskumpladen og på overholdelse af reglerne for dens installation.
Skumets holdbarhed blev detekteret i løbet af forskning, både i laboratorie og i naturlige forhold. Da udvidet polystyren i virkeligheden er plastik, forventes forskerne at få et højt holdbarhedsniveau. Under forskningen var deres forventninger fuldt berettiget.
Så udvidet polystyren er i stand til at bevare sin oprindelige termofysiske egenskaber i flere årtier uden at blive deformeret og uden at miste sin struktur. Det blev også fundet, at det er i stand til at modstå kortvarig udsættelse for lave (grænser -180ºі) og høje (+ 95ºС) temperaturer. Dette gør polystyrenskum til et ideelt isoleringsmateriale i det russiske klima og udvider også anvendelsesområdet for materialet - for eksempel lad os sige sin kontakt med smeltet bitumen.
Opførelsen af båden begynder med fremstilling af papirmønstre af alle side-, bund- og skotkrydsfiner. Derefter begynder de at skære krydsfiner, da alle stykker skal skæres langs fibrene i de ydre lag (skjorter). Der laves en lille godtgørelse til forarbejdning af enderne. Detaljer af sider og skotter skæres parvis. Derefter skæres lameller til langsgående og tværgående sæt. Arbejdsstykker skal mærkes med dobbelt nummerering: Det første ciffer er sektionsnummeret, og det andet er partinumret (for eksempel 3-11 osv.).
På mønstrene med en blyant sætte den præcise kontur og stedet for limning af detaljerne i sættet (laths). Begge overflader er smurt med lim, de presses mod lamellerne. Samlinger forbinder i halvtræet. For at beskytte mod glidning, tages hjørnerne midlertidigt med små negle (ikke fuldt ud). Umiddelbart inden limmen hærdet, blev perlen vendt om, og lamellerne blev fastgjort på krydsfinersiden med 2x10 "snake" skruer med en stigning på 50-60 mm. Billets til interne skotter og transom gør det samme. Til næsesektionen kan straight-line lameller ikke anvendes - de er lavet af limet krydsfiner. For at gøre dette skal du klippe 16 smalle (30-32 mm) strimler af krydsfiner 650 mm lang. På et tykt bord med en størrelse på 700x200 mm tegnes levetids konturer af den øverste (fri stråle) og nedre (zygomatic stringer) lameller. Konturen er fyldt med 75 mm negle til en dybde på 15-20 mm. Derefter smøres de tomme strimler med lim og indsættes i skabelonen dannet af negle. For at stramme strimlerne tættere under tørring, føres et garn gennem slangen i toppen af neglene. Det andet par blanke limes på samme måde. Kanten af de limede emner behandles med en fil og sandpapir.
En stamme (bøjlestang) hæves ud af en egetræ. Til fastsættelse af enderne af fenderne og de zygomatiske stringers i den gør sideskinner. Derefter forbindes de zygomatiske stringers, stamme og nasalskott sammen med lim og skruer, og toppen af stammen forbindes med toppen af skottet med en midlertidig strimmel på skruerne. Derefter sættes billetperler straks på lim og skruer, og hegnens emner er "pakket rundt" oven på dem. Det er nødvendigt at kontrollere symmetrien af hele strukturen.
På en dag, hvor limen "grasps", lægges der en bund og et dæk, hvor et hul på 180x200 mm til bagagelugen er forskåret. Derefter trækker man på et ark papir (helst grafpapir) et inde i de andre kvadrater og konturet af næsesektionen, svarende til størrelsen af den øvre del af den fremtidige båd - det vil gøre det lettere at sammenklare sektionerne og eliminere behovet for at korrigere forvrængningerne. På gulvet, på et ark papir - en skabelon, er alle sektioner samlet på lim og skruer - først sider og skotter, og derefter bundpladerne. Derefter monteres fenderne (med pigge og stikkontakter) og installeres, båden er midlertidigt monteret med bolte og behandlet og arkiveret med en fil og sandpapir. Denne operation skal udføres to gange.
Alle sektioner og emner af bundstrengere er imprægneret med hot linseed to gange. Efter den anden imprægnering inkuberes i 4-5 dage. De tørrede sektioner er let skrabet med sandpapir og igen sat sammen til den endelige kontrol af alle leddene. Derefter udslettes sektionerne udenfor med en vatpind dyppet i benzin eller hvid ånd for at affedt overfladen.
Derefter lægges bunden af alle fem sektioner over med glasdug på epoxylim med tilsætning af 10-15% acetone som fortyndingsmiddel. Tygets kanter foldes og sænkes til siderne med 50-80 mm. Samtidig fastsættes smalle strimler - skruer af glasfiber på samme epoxy lim alle yderste hjørner af sektionerne. Umiddelbart, inden harpiksen sættes, påføres en stringer smurt med samme lim på bunden og fastgøres med 3x15 skruer med en stigning på 80-100 mm.
To dage senere (48 timer) efter at harpiksen hærder, bliver båden igen behandlet med sprængpapir (især ved kanten af glasstof) og derefter malet med det første lag af maling. Efter at malingen er tørret, er alle metaldele installeret, kablet af slibekablet, montering af sæder (dåser) og lukkedækslet er færdige. Holdere af oarlocks fremstilles ved nitning af stykker af duralumin af passende tykkelse. I ekstreme tilfælde er den lavet af egetræ eller bøg træ med stålstrimler. Åre (sammenklappelig, sving) er lavet af tre stiklinger fra skovlerne, aluminiumsrør af passende diameter, tæt på hinanden og aluminiumsklinger 150x400x1,5 mm i størrelse. I den anden, tredje og fjerde sektion er det ønskeligt at lave lysvande langs længden af sektioner med en bredde på ca. 400 mm. De er lavet af skinner 10x15 mm med en stigning på 25 mm, forbundet med tre smalle tværgående dural striber.
Kablet er sikret med en sløjfe i strammeren fra transomens kølepunkt; så går det på begge sider af kølestrengen til stilken; På stammen krydser den to gange i rillerne under dækpladen og vender tilbage til agteren langs siderne under fenderen. Kabelens ender fastgøres i spænderne i de øvre hjørner af spidsen (lanyards). Tid til byggeri af båden vil tage omkring 150-200 timer (dette afhænger af amatørens snedkunst "kvalifikation").
firma
Skum egenskaber
Først og fremmest udsender de termiske egenskaber af skumplastik. Dette er et glimrende isoleringsmateriale, som bruges i næsten alle områder af opbygning af både industrielle og civile strukturer. Polystyrens varmeledningsevne er 3 gange mindre end for ekspanderet ler og træ og 17,5 gange lavere end murstenes varmeledningsevne.
Til sammenligning, hvis du tager 12 cm skum, svarer de til ca. 210 cm murstensarbejde. Sådanne termiske egenskaber ved polystyren kan betydeligt spare energi, som bruges til rumopvarmning. Derudover har dette materiale også fremragende lydisolerende egenskaber. Dette forklares primært af pladernes porøse struktur. Jo tykkere materialet er, des bedre er isoleringen.
Også en vigtig egenskab af skummet er dets modstand mod forskellige kemiske påvirkninger, da den er lavet af miljøvenlige komponenter. Det udgør ikke et miljø, der fremmer udviklingen af svamp og skimmelsvamp, så der er praktisk taget ingen problemer under driften. Og selvfølgelig er det umuligt ikke at notere dens fugtighed og brandmodstand.
Det opretholder ikke brænding. Men samtidig er han i stand til at udstede skadelige gasser (dette er hans ubestridelige minus).
Materialets holdbarhed og dets højstyrkeegenskaber gør det muligt at bruge det i konstruktionen af de mest seriøse bygninger og strukturer. Talrige tests har vist, at skummet er i stand til at modstå betydelige mekaniske belastninger og ikke deformeres. Og det passer simpelt nok, da det har en lille vægt.
karakteristika
Styrofoam og dens egenskaber
År for år øges omkostningerne ved opvarmning parallelt med de stigende energiforbrug. Og på samme tid, i den kolde årstid fordamper varmen bogstaveligt fra huset. Varmetab er virkelig enormt. Det store flertal af bygninger i Rusland, der ikke er opvarmet med beskyttende materialer, mister mere end 600 gigacalorier af varme pr. Kvadratmeter. Til sammenligning er den samme indikator i Tyskland lig med 40 gigacalories. Et materiale kaldet polystyren vil hjælpe med at løse problemet med store varme tab. Udvidet polystyren har et hele sæt egenskaber Så vi lister dem.
Varmeledningsevne
Materialet har fremragende varmeisoleringsegenskaber, primært på grund af strukturen. Strukturen af polystyren er et sæt bolde fastgjort sammen, der hver består af et stort antal celler med luft inde. Denne luft er ikke i stand til at bevæge sig, og at den udfører funktionen af en varmeisolator. Materialets termiske ledningsevne øges med stigende densitet. Polystyren bevarer sine egenskaber i temperaturområdet fra -50 til +75.
Fugtabsorption og dampgennemtrængelighed
Ekstruderet polystyren sammenlignet med polystyren har en langt højere dampgennemtrængelighed på grund af, at damp trænger ind i kuglerne, der danner grundlaget for materialet (og dermed i deres celler) langs siderne skåret under støbeprocessen (skummet er støbt uden skæring). Med fugtabsorption er alt lige præcist det modsatte: Fugtpermeabilitet er større, fordi skumpolystyren er tættere end skum.
styrke
På grund af tilstedeværelsen af stærkere bindinger mellem molekylerne af ekstruderet polystyrenskum, er dets styrke højere end skumets. Derfor bruges skum mindre og mindre.
Reaktion på organiske og kemiske produkter
Udvidet polystyren reagerer ikke på opløsninger af sæbe og salt, grundvand, emulsioner, mineralske gødninger, opløsninger baseret på gips, cement, bituminøse harpikser mv. Terpentin, acetone, tørringsolier og nogle typer lakker har en negativ virkning (op til opløsning). Ultraviolet er skadeligt for materialets åbne overflader - Styrken og elasticiteten under dens indflydelse går tabt. Skummet er ikke en undtagelse. Det begyndte straks at blive anvendt som isolering for at sikre oversvømmelighed, når der bygges glasfiberkar - til fremstilling af monteringsenheder. Men af en eller anden grund er skum ikke brugt som det vigtigste strukturelle materiale, selv om det efter min mening kan og bør laves små både, pendulkasser, tuziki og enkle hjemmelavede både. Lad mig minde om de vigtigste fordele ved skumplastik over de "traditionelle" materialer, der almindeligvis anvendes til konstruktion af sådanne både (vi taler ikke om termoplast, der endnu ikke er tilgængelige).
Polyfoam er let, har tilstrækkelig styrke, høje varmeisoleringskvaliteter, er godt skåret og savet (skum som PS-1 og PSBS er perfekt skåret med en nichrom-streng, der opvarmes ved at forbinde elektrisk strøm til den), godt limet. På den anden side er det umuligt at bøje skum. For at teste kapaciteterne i skumkvaliteten PS-1, gjorde jeg ham til en ikke-valgbar, ubøjelig robåd "Gamma", som med en vægt på ca. 20 kg har en lastkapacitet på 120 kg og er ret praktisk at betjene, især når man fisker i en bil. Bådens hovedmål: længden er den største, m 2.60 Bredde over pladens bredde, m 1.05 Bredde over bunden, m 0.78 Bordhøjde midtskår, m 0.38 Bordhøjde ved ekstremiteterne, m 0,40 Måder at lave en båd selv! Ved udformningen viste valget af skrogformen sig at være det sværeste: det var nødvendigt at lave en fleksibel, nem at gøre og bekvem lille båd ud af flade elementer. I sidste ende viste det sig at være en tuzik med en transom næse og akter, kælet forkant, skrånende (sammenbrudte) sider og en flad bund lidt forhøjet til agteren (sternfinen er indstillet her). Online butik fiskeri produkter.
Hjemmelavet båd. Sådan laver du et båd fra FOAM "Gamma" - en skumbåd En skumbåd (vi anbefaler at se hjemmelavede både) "Gamma" flydende. Normalt vurderer amatørskibsbyggere, når de møder med noget nyt materiale, først og fremmest udgangspunktet for anvendelighed til bygning af en båd. Polyfoam var ingen undtagelse. Det begyndte straks at blive anvendt som isolering for at sikre oversvømmelighed, når der bygges glasfiberkar - til fremstilling af monteringsenheder. Men af en eller anden grund er skum ikke brugt som det vigtigste strukturelle materiale, selv om småbåde, penduler og slæbebåde efter min mening kan og bør gøres af det. Lad mig minde om de vigtigste fordele ved skumplastik over de "traditionelle" materialer, der almindeligvis anvendes til konstruktion af sådanne både (vi taler ikke om termoplast, der endnu ikke er tilgængelige).
Polyfoam er let, har tilstrækkelig styrke, høje varmeisoleringskvaliteter, er godt skåret og savet (skum som PS-1 og PSBS er perfekt skåret med en nichrom-streng, der opvarmes ved at forbinde elektrisk strøm til den), godt limet. På den anden side er det umuligt at bøje skum. For at teste kapaciteterne i skumkvaliteten PS-1, gjorde jeg ham til en ikke-valgbar, ubøjelig robåd "Gamma", som med en vægt på ca. 20 kg har en lastkapacitet på 120 kg og er ret praktisk at betjene, især når man fisker i en bil. Bådens hovedmål: Længden er den største, m 2.60 Bredde på tværs af planbredden, m 1.05 Bredde over bunden, m 0.78 Bordhøjde midtskår, m 0.38 Bordhøjde ved ekstremiteterne, m 0.40 Ved design af det sværeste Det viste sig at være valget af skrogformen: det var nødvendigt at lave en bærbar, nem at fremstille og bekvem lille båd ud af flade elementer. I sidste ende viste det sig at være en tuzik med en transom næse og akter, kælet forkant, skrånende (sammenbrudte) sider og en flad bund lidt forhøjet til agteren (sternfinen er indstillet her).
Teoretisk tegning af skibets skrog fra skummet Teoretisk tegning af skibets skrog fra skummet Skæring af skibsdelene fra skummet Skæring af skibsdelene fra skummet. zoom 1248х2642, 326 KB I - agteromgang; II - bagsiden af siden (2 stykker); III - agterdel af bunden IV - bord (2 stk.); V - bund; VI - næse af perlen (2 stk.); VII - zygomatisk ark (2 stk.); VIII - nasal transom. Separate flade dele med en tykkelse på 30 mm udgør en monolitisk struktur efter limning. Transoms er lavet af et ark dobbelt så tykt og glat skrånende langs konturen. Sammenføjningskanterne på de dele, der skal tilsluttes, skæres i en vinkel, som vist på skissen. Dette giver en stigning i området med limning langs leddene og forenkler en smule skæring af plader, da der ikke er behov for at beregne dimensionerne for tykkelsen af forbindelsesdelen. Bådens konstruktion kan opdeles i tre faser: skæreark - fremstilling af skrogdele; monteringsdele på leddene - montage; limning og endelig efterbehandling. For mere effektiv anvendelse af materialet ved skæreark anbefaler jeg at skære mønster mønstre ud af tykt papir. Hvis du ikke har tillid til kantens rethed, skal kun en af dem skæres "i en vinkel"; Kanten, der går i forbindelse med den, skal tilpasses under montage. For at gøre det lettere at montere og montere, er det bedst at lave en bunke af fem par "tværgående" og to par "langsgående" kølblokke, der fastgør placeringen af bunden og siderne, såvel som bue- og agterspidsen. Pasta kan laves af enhver lim anbefales til polyfoam.
Jeg brugte epoxy lim baseret på ED-5 harpiks. Efter at limet helt har stået op, har han skærpet den frie kant af brættet og lagt en træperle på den omkring skrogets omkreds - en egestrimler på lim og skruer. For pålidelighed i alle hjørner og stødsamlinger på niveauet af perlenes øvre kant, udvendige pålagde en længdesnit af AMg legering (stribe 1.5X20, 130 mm lang, på siden fra leddets akse). Foderfinnen sat på bunden var også bundet med den samme strimmel. Efter tømning og afstrygning blev kappen belagt med nitro emalje på ydersiden og indeni. Denne beskyttelse viste sig at være praktisk nok, så det er helt muligt at gøre uden glasfiberlimning af skumet osv. De aftagelige dåser, der samtidig tjener som tværbindinger, brister sidene, er lavet af træ på Gamme. De bliver lettere, hvis de skæres ud af skumplast, ved at løbe rundt om kanterne af forstærkende træplader. Banker er hængt på siderne ved hjælp af clips - greb, bøjet fra aluminiumsskrot AMg. Rattet er hængt på stifterne, der er anbragt på den bageste omgang. Da jeg allerede begyndte at teste Gammaet, tvivlede jeg stadig på valget af materiale, der frygtede for skumkroppens styrke. Men med hver ny udgang fik jeg mere og mere tillid til min båd. Svømning i forskellige forhold, transport og trække med træk, når det er svært at udelukke alle slags slag, nogle gange meget stærke, viste, at båden er stærk (selvom den ikke er fastgjort af banker) og pålidelig. Og der er ikke noget at sige om oversvømmelighed: det er næsten umuligt at drukne Gamma. Der er en skumbåd (se fotoet hjemmelavede legetøjsbåde) og andre specifikke fordele. Den komplette mangel på rekruttering og enhver opslæmning hjælper med at holde båden indvendig ren. På grund af skumets gode varmeisoleringsegenskaber i båden kan du sidde direkte på bunden; når hun trækkes i land, sætter jeg mig der for natten uden at risikere forkølelse fra jorden. Når jeg anbefaler polystyren til at lave lyse tuzik shuttles, vil jeg nævne en af dens minus: den er bange for ild! Med andre ord skal man huske på, at ildens nærhed kan ødelægge din båd; selv berøring af en tændt cigaret smelter skummet.
Den teoretiske tegning er grundlaget for et båds projekt, og du kan ikke undvære det, når du bygger et skib. Tegnet på papir, er det imidlertid uegnet til byggearbejder: En lille skala fører til fejl ved måling og, vigtigst af alt, tillader ikke at markere sagens detaljer direkte.
Til konstruktion af skibets skrog skal teoretisk tegning ske i fuld størrelse. En sådan tegning kaldes en nedlægning eller et tegningstegning; Det er tegnet på et fladt trægulv eller på store krydsfinerplader - en plaza. Afvigelser, når du udfører en plaza og fjerner skabeloner fra den, må ikke overstige 1-2 mm. For at flytte fra en teoretisk tegning, lavet i designet til skalaen, til plasmaen en, er der opstillet et bord af gulvordinaterne. I denne tabel angives ordinaterne i fuld størrelse, det vil sige dimensionerne taget fra den teoretiske tegning multipliceres med dens skala. Ordinater er indstillet for alle buede linjer af en teoretisk tegning ved rammer og grupperet af fremskrivninger. Vandgruppen er givet højderne fra tungenes hovedlinje (kileformet hak i kølen og stænglen til kappepladerne, der holder fast ved dem), balder, dæk, kindben, køl; i den anden gruppe - halvbredder (fra diametralplanet, herefter - DP) af vandlinierne, kindbenet og siderne på dækket; ordinater af fisk. Nogle dimensioner, som dimensioner for konstruktionen af stænger og finner, er ikke medtaget i bordet af plasdordinater, men er normalt angivet på selve teorien.
Selvfølgelig skal du ved hjælp af bordet på ordinaterne vide, på hvilke afstande skæreplanerne er placeret en efter en, det vil sige afstanden mellem rammene er afstanden samt afstanden mellem vandlinierne og mellem balderne.
Det er kendt, at positionen af et hvilket som helst punkt i rummet er entydigt bestemt af tre koordinater i forhold til tre indbyrdes vinkelrette basisplaner. Ordinatbordet er et sæt koordinater, som bruges til at indstille placeringen af et stort antal punkter, der fastgør positionen af fartøjets skrogoverflade i rummet. Således kan i en meget bekvem tabulær form en vilkårlig kompleks tilfælde form "programmeres". Til konstruktionen af båden er der kun brug for en eneste projektion af den teoretiske tegning - "Kroppen" og omdrejningen af pivoten. Fremspringene til "Halvbredde" og "Side" anvendes kun til matchende linjer.
For at spare plads på pladsen kan du tegne fremspringene "Side" og "Semirashire" på den anden. Nå, hvis linjerne vil være forskellige farver. På korpsprojektionen skal grenene på højre og venstre side af rammen trækkes. Det er bedre at kombinere ribbenene (efter linjens farve) ind i bue- og agtergrupper (tæller fra midterdelen).
Brugen af en ukorrekt konstrueret teoretisk tegning kan føre til ændringer. Med en layoutafbrydelse kan bygherren trække enhver del af skroget på den i fuld størrelse. Der er få sådanne detaljer. Dette er først og fremmest kølen, stammen, hækbushen, transom, knopa, ideer og træstænger. Alt dette udgør fartøjets fane. Bogmærket skylder sit navn på, at når det er samlet, udgør det som det hele grundlaget for hele sættet - skelet på skibet. Kølens højde er normalt angivet på konstruktions tegningen i flere sektioner, bredden er taget under hensyntagen til halvbredden af tungen fra bordet af lægordinater. Korsets tværsnit, som enhver anden langsgående forbindelse, er let at bygge direkte på projektionsprojektionen på en teoretisk ramme. For at beregne tungen på stilken, skal du bruge en anden projektion - "Halvbredde", på hvilken sektioner af stammen langs vandlinierne præsenteres i deres egentlige form.
Ved hjælp af markeringen på pladsen fremstiller de skabeloner, hvor det er nemt at udforme detaljerne i bogmærket på træblanker og derefter behandle dem i en "ren størrelse", der svarer til den teoretiske tegning. Andre detaljer af en kompleks form er trukket på pladsen, for eksempel fundamentstænger til motoren (positionen af akselaksen skal først markeres), positionen af længderetningerne er angivet, og deres tværsnit på rammene er afbildet (om nødvendigt udskæringer til passage af strengere er lavet i det tværgående sæt).
Amatørbyggeren kan ikke altid tegne en teoretisk tegning af selv en lille båd, da det er nødvendigt at have et ret stort frit rum, passende redskaber: lange fleksible lameller - regler, klemmer - rotter til fastgørelse af buede skinner d. og vigtigst af alt - tilstrækkelige færdigheder. Med et bord af ordinater kan du begrænse dig til at nedbryde kun et, det mest nødvendige og små i projektionsprojektet - "Case", og lægge det på et ark tykt papir, som let kan foldes i en rulle og fjernes under brud på arbejdet. Hvis du på en sådan improviseret plaza også tegner en kontur af stammen og hældningsvinklen på transommet, vil dette være nok til at samle skroget.
Men man kan kun disponere over sammenbruddet af en enkelt "Case" -projeksion, hvis praktiske rammer er bygget på den teoretiske tegning, der er inkluderet i sæt af skibskroget. Hvis rammerne i den teoretiske tegning ikke falder sammen med de praktiske rammer, er det nødvendigt at bryde ind i pladsen mindst en yderligere projektion - "Halvbredde". Efter at have markeret placeringen af praktiske rammer på fremspringet af "halv bredde" i overensstemmelse med rammen defineret ved tegningstegningen (tegningen, som viser alle komponenter og detaljer af skrogkonstruktionen med grundlæggende dimensioner), fjern vandlinjekoordinaterne fra disse rammer på rammene og overfør dem til "Bolig" projektionen . For at modstå konturerne for konstruktionen af den teoretiske tegning (og først da skibets kvalitet og udseende vil matche det projicerede), er det nødvendigt at kende reglen om positionen af de teoretiske linjer for skrogets strukturelle elementer.
Den teoretiske linje er linien af strukturelementets overflade, som falder sammen med linien i den teoretiske tegning. Sådanne linjer til et træfartøj med en plank eller rackforing er:
ydre hudlinie Ved fremstilling af rammer, stubber og køler bør tykkelsen af huden deponeres indad fra de teoretiske linjer af disse elementer;
linjen på dækets indvendige overflade, med andre ord bjælkens overkant, som falder sammen med linjen af strålen i den teoretiske tegning
nakkestøtternes agterkanten og nakkestøtternes næsekant;
Ved fremstilling af rammer og skotter ved plasmaafbrydelse (minus tykkelsen af huden) er det nødvendigt at strengt følge reglen om teoretiske linjer og derefter fjerne perlerne (skære hjørnet), når du installerer huden, vil ikke ændre konturerne;
kanten af carling og stringers, reverseret af KDP.
Ved deling af plade af krydsfiner og plastbåde skal der normalt ikke tages hensyn til pladetykkelsen, dvs. rammerne af rammerne er også teoretiske linjer (ved afvigelse fra denne generelle regel i ordinatabellen skal der være en passende indikation). Alle teoretiske linjer med strukturelle elementer er gennemboret i en tegningstegning, og de nødvendige dimensioner og mønstre er allerede taget fra dem. At producere dele nøjagtigt ifølge layouttegning er ikke alt. Det er nødvendigt at sætte dem korrekt på plads, det vil sige rette alle detaljer, således at dets position i forhold til de tre referenceplaner: hoved (i højde), diametrisk (i bredde) og midtramme (fuld) - svarer strengt til den teoretiske tegning og plazma . Når man forbereder dele, overføres kontrollinjens position fra plating tegningen: DP, vandlinje eller eventuelle yderligere linjer parallelt med dem med angivelsen af afstanden til dem. Ægte, for eksempel er partiets position helt bestemt af nummeret på rammen; Hvis dette ikke er nok, er afstanden til nærmeste ramme angivet.
Hjemmelavet foldbar båd Matryoshka
"Matryoshka-båd" lavet af krydsfiner af L. Afrins design består af dele, der foldes ind i den anden under transport, som en dukkematryoshka (figur 1). En sådan båd er nem og bekvem at transportere, den kan transporteres med bus eller tog. Det er meget let at fremstille og vejer kun 12-17 kg. Indlæsningskapaciteten er 100-110 kg.
Fig. 1. Bådens design fra to sektioner: 1 - beklædning; 2,3,4 - detaljer af båden; 5 - rake
Til fremstilling af båden skal:
to ark med 4 mm krydsfiner størrelse 1525 x 1525 mm
bred fyrretræs tykkelse på 1,5-2 cm
tynde lameller
tin stripe 2-2,5 cm bred (kan skæres ud af dåser)
tørring af olie
olie maling
50mm negle.
For det første skæres to krydsfiner 1 og blanke 2, 3 og 4 ud af krydsfiner, efter at have været polstret med krydsfiner på begge sider. Klip ud emnerne og plader af krydsfiner i leddene er belagt med en tyk olie maling, lim "Phoenix", "Unikum" eller epoxy lim.
Derefter krydses krydsfinerhus 1 til dele 2, 3 og 4. For at forhindre chipping ved krydsfinerens kant, bores hullerne langs kanten af kappen med en Ø2 mm boremaskine. De bøjede og bøjle dele af båden er forbundet således, at bugten er fundet på agterbjælken med 3-4 cm. Samtlige ledd er dækket af tin striber, og inden møbelbeklædningen dækker de overfladen med tyk oliemaling. Herefter spik jernbanen på bunden af båden og lamellerne på siderne.
Den færdige båd behandles indvendigt og udad med varm linolie, og efter tørring er skibet dækket af to lag oliemaling på begge sider, forsigtigt forsegling af alle spalter og riller. Bådens bue er lavet af tæt konstruktion skum, hvis plader limes sammen med epoxy lim eller olie maling på naturlig tørring olie. Derefter dækkes bådens næse med to eller tre lag gasbind, gennemblødt dem med epoxylim eller olie maling på naturlig tørringsolie. Den færdige næse er fastgjort til næsepladen med to studsbolte. Foderdelen er også lavet af skumplast.
Åre i båden dobbelt, som på en kajak. Den samlede længde af padle er 220-240 cm. Du kan bruge færdige metal eller træ kajak paddles, som er kommercielt tilgængelige.
Normalt vurderer amatørskibsbyggere, når de møder med noget nyt materiale, først og fremmest udgangspunktet for anvendelighed til bygning af en båd. Polyfoam var ingen undtagelse. Det begyndte straks at blive anvendt som isolering for at sikre oversvømmelighed, når der bygges glasfiberkar - til fremstilling af monteringsenheder. Men for en eller anden grund er skum ikke brugt som det vigtigste strukturelle materiale, selv om det efter min mening kan og bør gøres af det.
Lad mig minde om de vigtigste fordele ved skumplastik over de "traditionelle" materialer, der almindeligvis anvendes til konstruktion af sådanne både (vi taler ikke om termoplast, der endnu ikke er tilgængelige). Polyfoam er let, har tilstrækkelig styrke, høje varmeisoleringskvaliteter, er godt skåret og savet (skum som PS-1 og PSBS er perfekt skåret med en nichrom-streng, der opvarmes ved at forbinde elektrisk strøm til den), godt limet. På den anden side er det umuligt at bøje skum.
For at teste kapaciteterne i skumkvaliteten PS-1, gjorde jeg ham til en ikke-valgbar, ubøjelig robåd "Gamma", som med en vægt på ca. 20 kg har en lastkapacitet på 120 kg og er ret praktisk at betjene, især når man fisker i en bil.
Ved udformningen viste valget af skrogformen sig at være det sværeste: det var nødvendigt at lave en fleksibel, nem at gøre og bekvem lille båd ud af flade elementer.
I sidste ende viste det sig skibet med skum med næsen og bagved, kælet forkant, skrånende sider (sammenbrudte) og en flad bund, lidt forhøjet til agteren (sternfinen er installeret her).
zoom, 1248х2642, 326 KB
I - Akterbøjle; II - bagsiden af siden (2 stykker); III - agterdel af bunden IV - bord (2 stk.); V - bund; VI - næse af perlen (2 stk.); VII - zygomatisk ark (2 stk.); VIII - nasal transom.
Separate flade dele med en tykkelse på 30 mm udgør en monolitisk struktur efter limning. Transoms er lavet af et ark dobbelt så tykt og glat skrånende langs konturen. Sammenføjningskanterne på de dele, der skal tilsluttes, skæres i en vinkel, som vist i. Dette giver en stigning i området med limning langs leddene og forenkler en smule skæring af plader, da der ikke er behov for at beregne dimensionerne for tykkelsen af forbindelsesdelen.
Skumbådens konstruktion kan opdeles i tre faser: skæreark - der gør kropsdele; monteringsdele på leddene - montage; limning og endelig efterbehandling.
For mere effektiv anvendelse af materialet ved skæreark anbefaler jeg at skære mønster mønstre ud af tykt papir. Efter skæring af alle dele langs kanterne, der skal tilsluttes, skal vinklen afskæres - afskæringen skal skæres til værdien n (se skitse ovenfor), som bestemmes af formlen afhængigt af den centrale vinkel a og tykkelsen af arket 6:
Hvis du ikke har tillid til kantens rethed, skal kun en af dem skæres "i en vinkel"; Kanten, der går i forbindelse med den, skal tilpasses under montage.
For at gøre det lettere at montere og montere, er det bedst at lave en bunke af fem par "tværgående" og to par "langsgående" kølblokke, der fastgør placeringen af bunden og siderne, såvel som bue- og agterspidsen.
Pasta kan laves af enhver lim anbefales til polyfoam. Jeg brugte epoxy lim baseret på ED-5 harpiks. Efter at limet helt har stået op, har han skærpet den frie kant af brættet og lagt en træperle på den omkring skrogets omkreds - en egestrimler på lim og skruer. For pålidelighed i alle hjørner og stødsamlinger på niveauet af perlenes øvre kant, udvendige pålagde en længdesnit af AMg legering (stribe 1.5X20, 130 mm lang, på siden fra leddets akse). Foderfinnen sat på bunden var også bundet med den samme strimmel.
Efter tømning og afstrygning blev kappen belagt med nitro emalje på ydersiden og indeni. Denne beskyttelse viste sig at være praktisk nok, så det er helt muligt at undlade at klæbe skummet med glasfiber osv.
Aftagelige krukker, der tjener samtidigt som krydsninger, arkiverer siderne, er lavet af træ på Gamme. De bliver lettere, hvis de skæres ud af skumplast, ved at løbe rundt om kanterne af forstærkende træplader. Banker er hængt på siderne ved hjælp af clips - greb, bøjet fra aluminiumsskrot AMg. Rattet er hængt på stifterne, der er anbragt på den bageste omgang.
Da jeg allerede begyndte at teste Gammaet, tvivlede jeg stadig på valget af materiale, der frygtede for skumkroppens styrke. Men med hver ny udgang fik jeg mere og mere tillid til min båd. Svømning i forskellige forhold, transport og trække med træk, når det er svært at udelukke alle slags slag, nogle gange meget stærke, viste, at båden er stærk (selvom den ikke er fastgjort af banker) og pålidelig. Og der er ikke noget at sige om oversvømmelighed: det er næsten umuligt at drukne Gamma. Skumbådet har andre specifikke fordele. Den komplette mangel på rekruttering og enhver opslæmning hjælper med at holde båden indvendig ren. På grund af skumets gode varmeisoleringsegenskaber i båden kan du sidde direkte på bunden; når hun trækkes i land, sætter jeg mig der for natten uden at risikere forkølelse fra jorden.
Når jeg anbefaler polystyren til at lave lyse tuzik shuttles, vil jeg nævne en af dens minus: den er bange for ild! Med andre ord skal man huske på, at ildens nærhed kan ødelægge din båd; selv berøring af en tændt cigaret smelter skummet.
Normalt vurderer amatørskibsbyggere, når de møder med noget nyt materiale, først og fremmest udgangspunktet for anvendelighed til bygning af en båd. Polyfoam var ingen undtagelse. Det begyndte straks at blive anvendt som isolering for at sikre oversvømmelighed, når der bygges glasfiberkar - til fremstilling af monteringsenheder. Men af en eller anden grund er skum ikke brugt som det vigtigste strukturelle materiale, selv om småbåde, penduler og slæbebåde efter min mening kan og bør gøres af det.
Lad mig minde om de vigtigste fordele ved skumplastik over de "traditionelle" materialer, der almindeligvis anvendes til konstruktion af sådanne både (vi taler ikke om termoplast, der endnu ikke er tilgængelige). Polyfoam er let, har tilstrækkelig styrke, høje varmeisoleringskvaliteter, er godt skåret og savet (skum som PS-1 og PSBS er perfekt skåret med en nichrom-streng, der opvarmes ved at forbinde elektrisk strøm til den), godt limet. På den anden side er det umuligt at bøje skum.
For at teste kapaciteterne i skumkvaliteten PS-1, gjorde jeg ham til en ikke-valgbar, ubøjelig robåd "Gamma", som med en vægt på ca. 20 kg har en lastkapacitet på 120 kg og er ret praktisk at betjene, især når man fisker i en bil.
Skumbådens hoveddimensioner
Maksimum længde, m 2,60
Bredde ifølge flymåler, m 1,05
Bundbredde, m 0,78
Board højde midship, m 0.38
Bordhøjde i ekstremiteter, m 0,40
Ved udformningen viste valget af skrogformen sig at være det sværeste: det var nødvendigt at lave en fleksibel, nem at gøre og bekvem lille båd ud af flade elementer.
I sidste ende viste det sig skibet med skum med næsen og bagved, kælet forkant, skrånende sider (sammenbrudte) og en flad bund, lidt forhøjet til agteren (sternfinen er installeret her).
Teoretisk tegning af skibets skrog
Skære skum dele
I - Akterbøjle; II - bagsiden af siden (2 stykker); III - agterdel af bunden IV - bord (2 stk.); V - bund; VI - næse af perlen (2 stk.); VII - zygomatisk ark (2 stk.); VIII - nasal transom.
Separate flade dele med en tykkelse på 30 mm udgør en monolitisk struktur efter limning. Transoms er lavet af et ark dobbelt så tykt og glat skrånende langs konturen. Sammenføjningskanterne på de dele, der skal tilsluttes, skæres i en vinkel, som vist i skitse af båden. Dette giver en stigning i området med limning langs leddene og forenkler en smule skæring af plader, da der ikke er behov for at beregne dimensionerne for tykkelsen af forbindelsesdelen.
Opførelsen af en skumbåd kan opdeles i tre faser: skæreark - fremstilling af skrogdele; monteringsdele på leddene - montage; limning og endelig efterbehandling.
Diagram af vinkelforbindelsen af dele.
For mere effektiv anvendelse af materialet ved skæreark anbefaler jeg at skære mønster mønstre ud af tykt papir. Efter skæring af alle dele langs kanterne, der skal tilsluttes, skal vinklen afskæres - afskæringen skal skæres til værdien n (se skitse ovenfor), som bestemmes af formlen afhængigt af den centrale vinkel a og tykkelsen af arket 6:
Hvis du ikke har tillid til kantens rethed, skal kun en af dem skæres "i en vinkel"; Kanten, der går i forbindelse med den, skal tilpasses under montage.
For at gøre det lettere at montere og montere, er det bedst at lave en bunke af fem par "tværgående" og to par "langsgående" kølblokke, der fastgør placeringen af bunden og siderne, såvel som bue- og agterspidsen.
Limet krop på lagrene.
Pasta kan laves af enhver lim anbefales til polyfoam. Jeg brugte epoxy lim baseret på ED-5 harpiks. Efter at limet helt har stået op, har han skærpet den frie kant af brættet og lagt en træperle på den omkring skrogets omkreds - en egestrimler på lim og skruer. For pålidelighed i alle hjørner og stødsamlinger på niveauet af perlenes øvre kant, udvendige pålagde en længdesnit af AMg legering (stribe 1.5X20, 130 mm lang, på siden fra leddets akse). Foderfinnen sat på bunden var også bundet med den samme strimmel.
Efter tømning og afstrygning blev kappen belagt med nitro emalje på ydersiden og indeni. Denne beskyttelse viste sig at være praktisk nok, så det er helt muligt at undlade at klæbe skummet med glasfiber osv.
Aftagelige krukker, der tjener samtidigt som krydsninger, arkiverer siderne, er lavet af træ på Gamme. De bliver lettere, hvis de skæres ud af skumplast, ved at løbe rundt om kanterne af forstærkende træplader. Banker er hængt på siderne ved hjælp af clips - greb, bøjet fra aluminiumsskrot AMg. Rattet er hængt på stifterne, der er anbragt på den bageste omgang.
Da jeg allerede begyndte at teste Gammaet, tvivlede jeg stadig på valget af materiale, der frygtede for skumkroppens styrke. Men med hver ny udgang fik jeg mere og mere tillid til min båd. Svømning i forskellige forhold, transport og trække med træk, når det er svært at udelukke alle slags slag, nogle gange meget stærke, viste, at båden er stærk (selvom den ikke er fastgjort af banker) og pålidelig. Og der er ikke noget at sige om oversvømmelighed: det er næsten umuligt at drukne Gamma. Skumbådet har andre specifikke fordele. Den komplette mangel på rekruttering og enhver opslæmning hjælper med at holde båden indvendig ren. På grund af skumets gode varmeisoleringsegenskaber i båden kan du sidde direkte på bunden; når hun trækkes i land, sætter jeg mig der for natten uden at risikere forkølelse fra jorden.
Når jeg anbefaler polystyren til at lave lyse tuzik shuttles, vil jeg nævne en af dens minus: den er bange for ild! Med andre ord skal man huske på, at ildens nærhed kan ødelægge din båd; selv berøring af en tændt cigaret smelter skummet.
Denne hjemmelavede skumbåd "fanget" fisk spænder fra landsbyen Rogozhkino på Nedre Don til Dry River under Tsimlyansk reservoiret; rejste næsten hele floden Manych og var på Veselovsky reservoir; besøgte Tuzlov-floden og Gorsky-floden af Don-floden mv.
Båden er lille og meget lys, let løftet og båret af en person. Udseendet af båden er ikke imponerende, men da jeg fiskede, spurgte fiskerne mig mange gange om, hvordan det blev lavet.
Det hele startede med ønsket om at få den nemmeste båd til at transportere med bil.
Jeg læser en masse magasiner "Både og Yachter" og besluttede at lave en båd i henhold til traditionelle anbefalinger ved at bygge et skrog af fiberplader, efterfulgt af at indsætte glasfiber på epoxyharpiks.
Skæremateriale fra fiberplader gik godt, bindingen med tråd gik værre, da hele strukturen gennemsøgte uden at holde den ønskede form.
Efter en vis brug af naturlig opfindsomhed viste den fremtidige båd smukt bunden af himlen.
Det er tid til at holde glasfiber.
Efter flere forsøg blev den bemærkelsesværdige konstruktion ødelagt med hidtil uset hastighed.
For at lime glasfiber med epoxyharpiks er det nødvendigt at have færdigheder, som jeg ikke havde, samt tankerne om at tjene penge ved at lave både.
På tidspunktet for den fremtidige båds ødelæggelse blev en meget enkel ide født i mit hoved, som hurtigt blev udformet i en materiel form.
Indholdet blev flyttet fra siden "Hjemmelavede både til fiskeri" dræbt til døden
Forventet seriøs redigering.
I dag er maj 2016
Hvordan man laver en båd ud af skum med egne hænder
Skumplader blev købt og er kun til salg, byggeskum.
Skummet blev skåret i ønskede stykker, snoede skruer og lim skummet.
Resultatet er fantastisk.
Skumbåd:
- absolut usynlig,
- vejer meget lidt
- lys på årer.
Båden er ikke meget smuk :), men det vigtige er ikke den skønhed og den praktiske virkning.
Det er sandsynligt, at historien vil skubbe nogens sind i den rigtige retning.
Båd i lang tid liggende rundt i gården. Det er sandsynligt, at det er mere nyttigt.
- Bådens længde er 260 cm.
- Stykkehøjde 34 cm.
- Bredde 100 cm.
- Skumtykkelse: bord 50 mm. bund 70 mm.
I agterenden og buen blev de fastgjort med skruer bord. De er rådne af gammel alder.
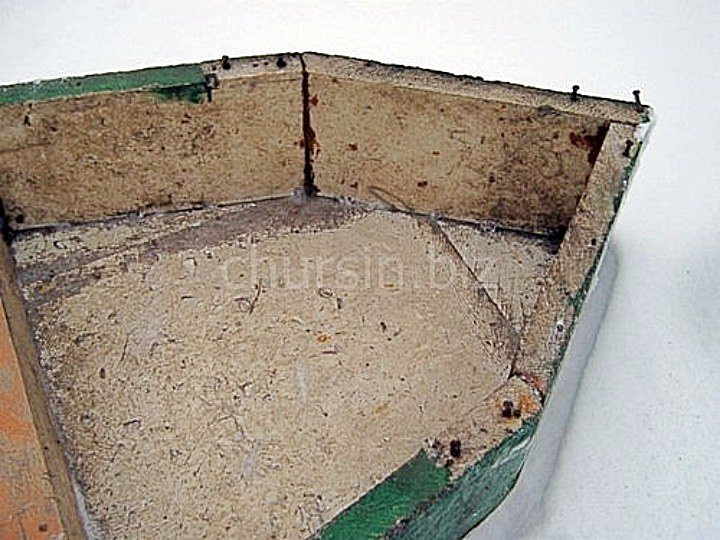

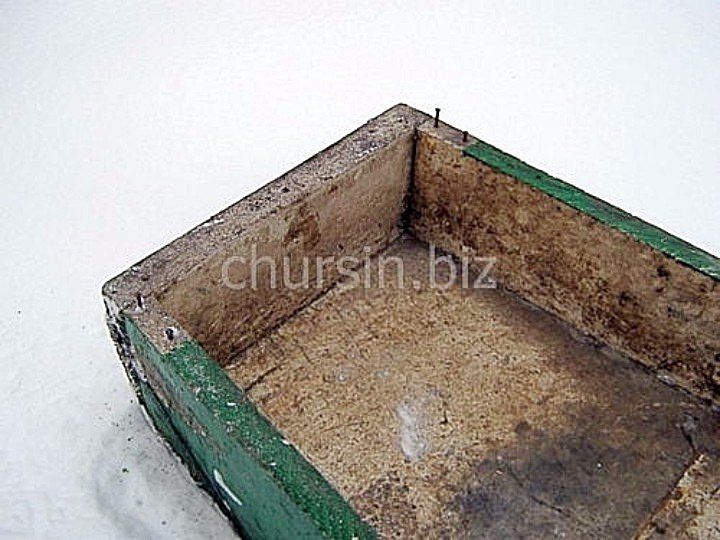