Cómo construir un video de espuma en barco. Bote de espuma
El problema de un pequeño bote de pesca se resolvió inesperadamente de manera simple. Tenía un plástico de espuma que anteriormente servía como tapicería de una casa antigua. Al estar familiarizado con la tecnología de construcción de un bote de espuma, sabiendo el proceso de pegar el casco con fibra de vidrio, seguí investigando "Botes y yates" y, para mi sorpresa, descubrí que la descripción de un bote de este tipo solo se encontró en 1975. Considero que la falta de atención a tales barcos es inmerecida, ya que tiene una serie de ventajas innegables como la espuma de plástico. En el barco hace calor, no hace ruido, lo que es importante cuando se pesca, tiene un peso bajo y una gran reserva de flotabilidad. El proceso de construcción es simple y toma un poco de tiempo.
Datos básicos del barco
El barco "Gamma", construido por Yu. Nikiforov, no me era adecuado debido a la complejidad del diseño. Para tal barco, es suficiente tener contornos más simples, con un plano, sin levantar, la parte inferior y la nariz del travesaño. La declaración de Yu. Nikiforov con respecto a la explotación del cuerpo de espuma "desnuda", sin pegado de fibra de vidrio, también estaba en duda. En base a estas consideraciones, construí un bote utilizando la siguiente tecnología en pocos días a partir de la espuma de PVC. Primero corté y conduje tres grandes láminas de espuma. De ellos se pegó el fondo. Luego, utilizando el soporte, similar al bloque de quilla "Gamma", se realizó el ensamblaje final del casco. Las placas de espuma de 40 mm de espesor se unieron entre sí con pegamento epoxi a base de resina ED-5.
El PVC de poliestireno se puede reemplazar por otro grado: PS-1 o PSBS. También cortaron bien con un cuchillo afilado y cortaron con una sierra para metales. Yu. Nikiforov cortó una cuerda de nicrom plástica de espuma, calentada conectándola a la red eléctrica. Sin embargo, debe tenerse en cuenta que las espumas de PS que contienen estireno se disuelven con resinas de poliéster, por lo tanto, es posible pegar partes del cuerpo o pegarlo con fibra de vidrio solo en un aglutinante a base de epoxi.
El cuerpo sin envoltura de fibra de vidrio pesa 20 kg, sin embargo, la operación de tal bote requerirá mucho cuidado, ya que la espuma se desgastará rápidamente e incluso un toque de un cigarrillo encendido puede arruinar a su hijo. Para darle al cuerpo mayor rigidez y fuerza, en este caso, debes poner un par de latas, rompiendo el costado. A lo largo del perímetro de la caja es necesario fijar una barra de roble - brida en la cola y los tornillos. No debe ser superfluo y dos tiras en la parte inferior, que lo protegerán de la abrasión al tirar del barco a la orilla. También es necesario proteger las juntas a tope fuera de la caja, pegándolas, por ejemplo, con tiras de tela.
Decidimos pegar sobre el estuche exterior con fibra de vidrio. El peso del casco aumentó ligeramente, pero la durabilidad de la embarcación aumentó.
En lugar de un frasco, uso un plato de espuma de altura pequeña: sentado sobre él, estoy protegido por los lados del viento. El bote va bien debajo de los remos, se cuela fácilmente en las cañas, gracias a unos contornos nasales bastante afilados.
Remos de aproximadamente 2 m de largo con cuchillas planas de 350X150 mm - tipo kayak. Para usar el motor fueraborda, el travesaño debe ser reforzado, como se muestra en el diagrama.
Por lo general, los constructores de barcos aficionados, cuando se reúnen con cualquier material nuevo, lo evalúan principalmente desde el punto de vista de la aplicabilidad para construir un barco. Polyfoam no fue una excepción. Inmediatamente comenzó a utilizarse como aislamiento, para garantizar la inundabilidad, cuando se construyen recipientes de fibra de vidrio, para la fabricación de unidades de ensamblaje. Pero por alguna razón, la espuma no se utiliza como material estructural principal, aunque, en mi opinión, los botes pequeños, lanzaderas y remolcadores, pueden y deben estar hechos de ella.
Instrucción
Propiedades de la espuma y poliestireno expandido.
Alto aislamiento térmico. En términos de retención de calor, la espuma de plástico supera a la mayoría de los materiales de aislamiento.
Ligereza Con toda su eficacia, la espuma plástica pesa sorprendentemente poco, ya que el 98% de su masa es aire. Si compara el poliestireno expandido en esta propiedad con otros materiales aislantes, se obtiene la siguiente proporción:
La placa de espuma de 50 mm de espesor es:
. 100 mm de lana mineral;
. o 200 mm de madera;
. o 325 mm de arcilla expandida;
. o ladrillos de 900 mm;
. o 1400 mm de hormigón.
De esto resulta que el aislamiento de la espuma, teniendo en cuenta el trabajo de instalación, cuesta entre 20 y 50 veces menos que el aislamiento de otros materiales. ¡Y su uso ahorrará algo más de dinero en calefacción!
Propiedades de la espuma
Amabilidad ambiental. Absolutamente seguro, por lo tanto, también se utiliza en la industria alimentaria. La espuma de poliestireno previene la formación de bacterias y moho. Se puede utilizar libremente a temperaturas: de - 60 a + 80 grados.
Seguridad Se reconoce que durante la combustión, la espuma emitirá los mismos elementos que la madera quemada. Y las últimas mejoras nos permiten dotar a la espuma de resistencia al fuego. La sustancia incluida en la espuma de plástico ignífuga previene la combustión y promueve la auto-extinción. Pertenece al grupo de inflamabilidad G4.
Resistente al agua. La espuma durante el año absorbe de 1.5 a 3.5% de humedad. Eso habla de su alto nivel de resistencia a la humedad. Vale la pena señalar el hecho de que existe una relación directa entre la transpirabilidad y la resistencia a la humedad de la espuma. La primera característica realza la segunda. Esta propiedad permite a las casas "respirar".
Fuerza Bajo la influencia de cargas mecánicas en espuma de plástico - espuma de poliestireno, se observa una reacción viscoelástica, que garantiza su alta resistencia. Su resistencia a la compresión es de al menos 0.04-0.20 MPa. Al mismo tiempo, el material conserva su tamaño original y no cambia la ubicación.
Aislamiento acústico. El acabado de espuma permite aumentar la protección contra el ruido externo en 2-4 dB.
Equipo
Tecnología de fabricación de espuma de polietileno
La base de la espuma es el poliestireno, un polímero termoplástico. Debido a su resistencia al agua, la capacidad de tomar cualquier forma bajo la influencia de la temperatura, la resistencia a las heladas, el poliestireno es ampliamente utilizado en la industria (caso de uso: creación de un recipiente para yogur). Sin embargo, el poliestireno sigue siendo nepoplast.
Se produce espumando gránulos de poliestireno. Después de la formación de espuma, se tratan con vapor de agua calentado, después de lo cual se repite todo el procedimiento.
Los procesos de espumación cíclica pueden reducir significativamente la densidad de los gránulos de poliestireno, lo que conduce a una disminución de su peso. Después de la formación de espuma secundaria, la espuma debe secarse. El secado es la eliminación de la humedad residual de la superficie de la espuma de poliestireno (el agua no ingresa al interior, el material impermeable a la espuma).
El secado se realiza al aire libre; es en esta etapa que el aire llena los poros del material y adquiere una forma completa. El tamaño de los gránulos puede variar de 5 a 15 milímetros.
El poliestireno expandido seco necesita moldeado. El material procesado se prensa con máquinas especiales y se somete a un tratamiento terciario con vapor caliente. Como resultado de la moldura, parece un bloque de color blanco de un cierto grosor. El bloque se corta en los formularios requeridos y en este formulario se envía al cliente.
Importante: la espuma se puede cortar no solo de acuerdo con los parámetros típicos, sino también de acuerdo con las dimensiones individuales requeridas para una construcción en particular.
El corte con espuma de poliestireno se realiza en máquinas con corte horizontal y vertical. Cuando el corte de su estructura no está dañado, el moldeo es rápido. La única condición tecnológica: la temperatura en el taller, donde se realiza el corte, no debe caer por debajo de 18ºС, de lo contrario, la espuma se romperá (desmenuzará).
Otra característica de la producción: la tecnología en sí, y las materias primas son relativamente baratas, lo que puede reducir significativamente el costo del producto final. Es seguro decir que la espuma no solo es un aislamiento seguro y confiable, sino que también es uno de los más baratos.
El bajo precio del material en combinación con su funcionalidad lo hace especialmente popular en ingeniería civil.
Hazlo tu mismo
Durabilidad y durabilidad de espuma de polietileno.
La espuma no tiene una densidad alta (50 veces menor que la del agua), pero, sin embargo, muestra una excelente resistencia a cargas mecánicas uniformes, tanto en tensión como en compresión.
Polyfoam es capaz de soportar la presión durante años sin deformarse, sin colapsar y sin cambiar sus propiedades físicas. Una ilustración vívida puede ser su uso generalizado en la construcción de pistas. El índice de resistencia depende en gran medida del grosor de la placa de espuma de poliestireno y del cumplimiento de las normas de su instalación.
La durabilidad de la espuma se detectó en el curso de la investigación, tanto en laboratorio como en condiciones naturales. Dado que el poliestireno expandido es, de hecho, plástico, los científicos esperan obtener altos niveles de durabilidad. Durante la investigación, sus expectativas fueron plenamente justificadas.
Así, el poliestireno expandido es capaz de retener sus propiedades termofísicas originales durante varias décadas, sin deformarse y sin perder su estructura. También se encontró que es capaz de soportar la exposición a corto plazo a temperaturas bajas (límite -180ºС) y altas (+ 95ºС). Esto hace que la espuma de poliestireno sea un material aislante ideal en el clima ruso, y también amplía el alcance del uso del material, por ejemplo, digamos su contacto con el betún fundido.
La construcción de la embarcación comienza con la fabricación de patrones de papel de todas las partes de madera contrachapada lateral, inferior y de mamparo. Después de eso, comienzan a cortar el contrachapado, dado que todas las piezas deben cortarse a lo largo de las fibras de las capas exteriores (camisas). Se hace un pequeño margen para procesar los fines. Los detalles de los lados y mamparos se cortan en pares. Luego se cortan las lamas por juego longitudinal y transversal. Las piezas de trabajo deben estar marcadas con una numeración doble: el primer dígito es el número de la sección y el segundo es el número de la parte (por ejemplo, 3-11, etc.).
En los patrones con un lápiz coloque el contorno exacto y el lugar de pegar los detalles del conjunto (listones). Ambas superficies están manchadas con pegamento, se presionan contra los listones. Las articulaciones se conectan en el semirbol. Para protegerse contra deslizamientos, las esquinas se agarran temporalmente con clavos pequeños (no completamente). Inmediatamente, hasta que el pegamento se endureció, la tabla se volcó y fortaleció las tablillas desde el lado de madera contrachapada con 2x10 tornillos de "serpiente" con un paso de 50-60 mm Los billetes para mamparos internos y travesaños hacen lo mismo. Para la sección nasal, los listones de línea recta no se pueden aplicar, están hechos de madera contrachapada encolada. Para ello, corte 16 tiras estrechas (30-32 mm) de madera contrachapada de 650 mm de largo. En una tabla gruesa con un tamaño de 700x200 mm, se dibujan contornos de tamaño natural de los listones superiores (viga libre) y más bajos (largueros cigomáticos). El contorno se rellena con clavos de 75 mm hasta una profundidad de 15-20 mm. Luego, las tiras en blanco se untan con pegamento y se insertan en la plantilla formada por clavos. Para apretar más las tiras durante el secado, se pasa una cuerda a través de la serpiente en la parte superior de las uñas. El segundo par de espacios en blanco se pegan de la misma manera. Los bordes de los espacios en blanco pegados se procesan con un archivo y papel de lija.
Un tallo (barra de arco) se corta de una barra de roble. Para fijar los extremos de los guardabarros y los largueros cigomáticos en ellos hacen surcos laterales. Luego, los largueros cigomáticos, el vástago y el mamparo nasal se unen con pegamento y tornillos, y la parte superior del vástago se conecta a la parte superior del mamparo con una tira temporal en los tornillos. Después de eso, las cuentas de palanquilla se colocan inmediatamente en pegamento y tornillos, y los espacios en blanco de las vallas se "envuelven" encima de ellas. Es necesario verificar la simetría de toda la estructura.
En un día, cuando el pegamento "agarra", un fondo y una cubierta se colocan en el que un agujero de 180x200 mm para la escotilla de equipaje es precortado. Luego, en una hoja de papel (preferiblemente papel cuadriculado) dibuje uno dentro de los otros cuadrados y el contorno de la sección nasal, correspondiente al tamaño de la sección superior del futuro bote; esto hará que sea más fácil pegar las secciones y eliminar la necesidad de corregir las distorsiones. En el suelo, en una hoja de papel, una plantilla, todas las secciones se ensamblan con pegamento y tornillos, primero los lados y los mamparos, y luego las hojas inferiores. Después de eso, se montan e instalan los guardabarros (con clavos y zócalos), el barco se ensambla temporalmente con pernos y se trata y archiva con una lima y papel de lija. Esta operación se debe realizar dos veces.
Todas las secciones y los espacios en blanco de los largueros inferiores están impregnados con linaza caliente dos veces. Después de la segunda impregnación, se incuba durante 4-5 días. Las secciones secas se raspan ligeramente con papel de lija y una vez más se juntan para el control final de todas las juntas. Luego, las secciones exteriores se limpian con un hisopo sumergido en gasolina o alcohol blanco para desengrasar la superficie.
Después de eso, los fondos de las cinco secciones se pegan con un paño de vidrio sobre pegamento epoxi con la adición de un 10-15% de acetona como diluyente. Los bordes de la tela se doblan y se bajan a los lados en 50-80 mm. Al mismo tiempo, tiras estrechas: trozos de fibra de vidrio en el mismo pegamento epoxi fijan todas las esquinas exteriores de las secciones. Inmediatamente, antes de que se establezca la resina, se aplica un tirante con el mismo pegamento en la parte inferior y se fija con 3x15 tornillos con un paso de 80-100 mm.
Dos días después (48 horas) después de que la resina se endurece, el bote se trata nuevamente con papel de lija (especialmente en el borde de la tela de vidrio) y luego se pinta con la primera capa de pintura. Después de que la pintura se haya secado, se instalan todas las partes metálicas, se realiza el cableado del cable de amarre, el ajuste de los asientos (latas) y la cubierta de la escotilla. Los soportes de oarlocks se fabrican mediante remachado de piezas de duraluminio de espesor adecuado. En el caso extremo, está hecho de madera de roble o haya con una tira de acero. Los remos (plegables, giratorios) están hechos de tres cortes de las palas, tubos de aluminio de diámetro adecuado, que encajan firmemente uno en el otro, y hojas de aluminio de tamaño 150x400x1.5 mm. En la segunda, tercera y cuarta secciones, es conveniente hacer una marea ligera a lo largo de las secciones con un ancho de aproximadamente 400 mm. Están hechos de rieles de 10x15 mm con un paso de 25 mm, conectados por tres estrechas rayas durales transversales.
El cable está asegurado por un bucle en el tensor desde el punto de quilla del travesaño; luego va a ambos lados del larguero de la quilla hasta el tallo; en el vástago, cruza dos veces las ranuras debajo de la placa de la cubierta y regresa a la popa a lo largo de los lados debajo del guardabarros; los extremos del cable están fijos en los tensores en las esquinas superiores del travesaño (cuerdas de seguridad). El tiempo para la construcción del barco durará entre 150 y 200 horas (esto depende de la "calificación" de la carpintería de un aficionado).
Las empresas
Propiedades de la espuma
En primer lugar, emiten propiedades térmicas de espuma plástica. Este es un excelente material aislante, que se utiliza en casi todas las áreas de construcción de estructuras industriales y civiles. La conductividad térmica del poliestireno es 3 veces menor que la de la arcilla expandida y la madera, y 17.5 veces más baja que la conductividad térmica de los ladrillos.
A modo de comparación, si toma 12 cm de espuma, son iguales a unos 210 cm de ladrillo. Estas características térmicas del poliestireno pueden ahorrar significativamente energía, que se gasta en calefacción de espacios. Además, este material también tiene excelentes propiedades de aislamiento acústico. Esto se explica principalmente por la estructura porosa de las placas. Cuanto más grueso sea el material, mejor será el aislamiento.
También una propiedad importante de la espuma es su resistencia a diversas influencias químicas, ya que está hecha de componentes ecológicos. No forma un entorno propicio para el desarrollo de hongos y moho, por lo que prácticamente no hay problemas durante la operación. Y, por supuesto, es imposible no notar su humedad y su resistencia al fuego.
No sostiene la quema. Pero al mismo tiempo es capaz de emitir gases nocivos (este es su indiscutible inconveniente).
La durabilidad del material y sus características de alta resistencia le permiten ser utilizado en la construcción de los edificios y estructuras más serios. Numerosas pruebas han demostrado que la espuma es capaz de soportar cargas mecánicas significativas y no está deformada. Y encaja lo suficiente, ya que tiene un peso pequeño.
Caracteristicas
Espuma de poliestireno y sus propiedades
Año tras año, el costo de la calefacción aumenta en paralelo con el costo creciente de la energía. Y al mismo tiempo, en la estación fría, el calor se evapora literalmente de la casa. La pérdida de calor es realmente enorme. La gran mayoría de los edificios en Rusia que no están calentados con materiales de protección pierden más de 600 gigacalorías de calor por metro cuadrado. Para comparación, en Alemania el mismo indicador es igual a 40 gigacalorías. Un material llamado poliestireno ayudará a resolver el problema de las enormes pérdidas de calor. El poliestireno expandido tiene un conjunto completo de características Por lo tanto, los enumeramos.
Conductividad del calor
El material tiene excelentes propiedades de aislamiento térmico, principalmente debido a la estructura. La estructura del poliestireno es un conjunto de bolas unidas entre sí, cada una de las cuales consta de un gran número de células con aire en el interior. Este aire no puede moverse y realiza la función de un aislante térmico. La conductividad térmica del material aumenta al aumentar su densidad. El poliestireno conserva sus características en el rango de temperatura de -50 a +75.
Absorción de humedad y permeabilidad al vapor.
El poliestireno extruido comparado con el poliestireno tiene una permeabilidad al vapor mucho mayor debido al hecho de que el vapor penetra en las bolas que forman la base del material (y, por lo tanto, en sus celdas) a lo largo de los lados cortados durante el proceso de moldeo (la espuma se moldea sin cortar). Con la absorción de humedad, todo es exactamente lo contrario: la permeabilidad a la humedad es mayor, porque la espuma de poliestireno es más densa que la espuma.
Fuerza
Debido a la presencia de enlaces más fuertes entre las moléculas de espuma de poliestireno extruido, su resistencia es mayor que la de la espuma. Es por eso que la espuma se usa cada vez menos.
Reacción a productos orgánicos y químicos.
El poliestireno expandido no reacciona a las soluciones de jabón y sal, aguas subterráneas, emulsiones, fertilizantes minerales, soluciones a base de yeso, cemento, resinas bituminosas, etc. La trementina, la acetona, los aceites de secado y algunos tipos de barnices tienen un efecto negativo (hasta la disolución). El ultravioleta es perjudicial para las superficies abiertas del material: la fuerza y la elasticidad bajo su influencia se pierden. La espuma no es una excepción. Inmediatamente comenzó a utilizarse como aislamiento, para garantizar la inundabilidad, cuando se construyen recipientes de fibra de vidrio, para la fabricación de unidades de ensamblaje. Pero por alguna razón, la espuma no se usa como material estructural principal, aunque, en mi opinión, los botes pequeños, los transbordadores, los tuziki y los botes simples hechos en casa pueden y deben estar hechos de él. Permítame recordarle las principales ventajas del plástico de espuma en comparación con los materiales "tradicionales" que se utilizan comúnmente para la construcción de este tipo de barcos (no hablaremos de termoplásticos que aún no están disponibles).
Polyfoam es liviano, tiene suficiente resistencia, alta calidad de aislamiento térmico, está bien cortado y aserrado (las espumas como PS-1 y PSBS se cortan perfectamente con una cuerda de nicrom calentada mediante la conexión de corriente eléctrica), bien pegadas. Por otro lado, es imposible doblar la espuma. Para probar las capacidades del PS-1 de grado de espuma, le hice un bote de remo no sumergible no seleccionable "Gamma", que, con un peso de aproximadamente 20 kg, tiene una capacidad de carga de 120 kg y es muy conveniente de operar, especialmente cuando se pesca en un automóvil. Dimensiones principales de la embarcación: la longitud es la más grande, m 2.60 Ancho a través del ancho de la placa, m 1.05 Ancho a través de la parte inferior, m 0.78 en medio del barco, m 0.38 Altura de la tabla en las extremidades, m 0.40 Formas de hacer un barco por ti mismo! En el diseño, la elección de la forma del casco resultó ser lo más difícil: era necesario hacer un pequeño bote de elementos planos, flexible, fácil de hacer y conveniente. Al final, resultó ser un tuzik con una nariz de popa y popa, parte delantera con quilla, lados inclinados (con colapso) y un fondo plano ligeramente elevado a la popa (aquí se establece la aleta de popa). Tienda online de productos de pesca.
Barco hecho en casa. CÓMO HACER UN BARCO CON ESPUMA “Gamma” - un barco de espuma Un barco de espuma (recomendamos ver barcos caseros) “Gamma” a flote. Por lo general, los constructores de barcos aficionados, cuando se reúnen con cualquier material nuevo, lo evalúan principalmente desde el punto de vista de la aplicabilidad para construir un barco. Polyfoam no fue una excepción. Inmediatamente comenzó a utilizarse como aislamiento, para garantizar la inundabilidad, cuando se construyen recipientes de fibra de vidrio, para la fabricación de unidades de ensamblaje. Pero por alguna razón, la espuma no se utiliza como material estructural principal, aunque, en mi opinión, los botes pequeños, lanzaderas y remolcadores, pueden y deben estar hechos de ella. Permítame recordarle las principales ventajas del plástico de espuma en comparación con los materiales "tradicionales" que se utilizan comúnmente para la construcción de este tipo de barcos (no hablaremos de termoplásticos que aún no están disponibles).
Polyfoam es liviano, tiene suficiente resistencia, alta calidad de aislamiento térmico, está bien cortado y aserrado (las espumas como PS-1 y PSBS se cortan perfectamente con una cuerda de nicrom calentada mediante la conexión de corriente eléctrica), bien pegadas. Por otro lado, es imposible doblar la espuma. Para probar las capacidades del PS-1 de grado de espuma, le hice un bote de remo no sumergible no seleccionable "Gamma", que, con un peso de aproximadamente 20 kg, tiene una capacidad de carga de 120 kg y es muy conveniente de operar, especialmente cuando se pesca en un automóvil. Dimensiones principales de la embarcación: la longitud es la más grande, m 2.60 Ancho a través del ancho del plan, m 1.05 Ancho a través de la parte inferior, m 0.78 en medio del barco, m 0.38 Altura del tablero en las extremidades, m 0.40 Cuando se diseña lo más difícil Resultó ser la elección de la forma del casco: era necesario hacer un pequeño bote de elementos planos portátil, fácil de fabricar y conveniente. Al final, resultó ser un tuzik con una nariz de popa y popa, parte delantera con quilla, lados inclinados (con colapso) y un fondo plano ligeramente elevado a la popa (aquí se establece la aleta de popa).
Dibujo teórico del casco de la embarcación a partir de la espuma Dibujo teórico del casco de la embarcación a partir de la espuma Corte de las piezas de la embarcación a partir de la espuma Corte de las piezas de la embarcación a partir de la espuma. zoom 1248х2642, 326 KB I - travesaño de popa; II - a popa del costado (2 piezas); III - parte de popa del fondo; IV - tablero (2 piezas); V - abajo; VI - la nariz de la cuenta (2 uds.); VII - lámina cigomática (2 piezas); VIII - popa nasal. Las partes planas separadas con un grosor de 30 mm forman una estructura monolítica después del pegado. Los travesaños están hechos de una hoja dos veces más gruesa y suavemente inclinada a lo largo del contorno. Los bordes de unión de las partes a unir se cortan en ángulo, como se muestra en el boceto. Esto da un aumento en el área de pegado a lo largo de las uniones y simplifica de alguna manera el corte de las hojas, ya que no hay necesidad de volver a calcular las dimensiones para el grosor de la pieza de conexión. La construcción del barco se puede dividir en tres etapas: láminas de corte: fabricación de piezas de casco; piezas de montaje en las juntas - montaje; Unión y acabado final. Para un uso más eficiente del material al cortar hojas, recomiendo cortar patrones de papel grueso. Si no confía en la rectitud de los bordes, solo uno de ellos debe cortarse "en ángulo"; El borde que lo une tendrá que ser personalizado durante el montaje. Para la conveniencia de la instalación y el montaje, es mejor hacer una pila de cinco pares de bloques de quilla "transversales" y dos pares de "longitudinales", fijando la posición del fondo y los lados, así como el travesaño de proa y popa. El pegado puede hacerse con cualquier pegamento recomendado para espuma de polietileno.
Usé pegamento epoxi a base de resina ED-5. Después de que el pegamento se haya levantado completamente, afiló el borde libre del tablero y colocó una cuenta de madera alrededor del perímetro del casco, una tira de roble sobre el pegamento y los tornillos. Para mayor confiabilidad en todas las esquinas y juntas a tope en el nivel del borde superior del talón, afuera impuso unas tiras longitudinales hechas de aleación AMg (tira 1.5X20, 130 mm de largo, en el lado desde el eje de la junta). La aleta de forraje colocada en la parte inferior también estaba unida con la misma tira. Después de la aplicación de masilla y pelado, la cubierta se recubrió con esmalte nitro en el exterior y el interior. Esta protección resultó ser prácticamente suficiente, por lo que es posible prescindir del pegado de fibra de vidrio de la espuma, etc. Las latas extraíbles, que al mismo tiempo sirven como enlaces cruzados, reventando los lados, están hechas de madera en el Gamme. Serán más fáciles si se recortan de espuma plástica, al correr alrededor de los bordes de los listones de madera de refuerzo. Los bancos se cuelgan en los lados con la ayuda de clips - empuñaduras, dobladas de trozos de aleación AMg. El volante se cuelga de los pasadores y se fija en el espejo de popa. Habiendo comenzado ya a probar el Gamma, todavía dudaba de la exactitud de la elección del material, temiendo por la resistencia del cuerpo de espuma. Sin embargo, con cada nueva salida gané más y más confianza en mi barco. Nadar en una variedad de condiciones, transportar y arrastrar con resistencia, cuando es difícil excluir todo tipo de golpes, a veces muy fuerte, mostró que el barco es fuerte (incluso cuando no está arreglado por bancos) y confiable. Y no hay nada que decir sobre la capacidad de inundación: es casi imposible ahogar a Gamma. Hay un bote de espuma (ver fotos de botes de juguete hechos en casa) y otras ventajas específicas. La falta completa de reclutamiento y cualquier lodo ayuda a mantener limpio el interior del barco. Debido a las buenas cualidades de aislamiento térmico de la espuma en el barco, puede sentarse directamente en la parte inferior; cuando la sacan a tierra, me quedo allí para pasar la noche sin arriesgarme a resfriarme del suelo. Cuando recomiendo el poliestireno para hacer lanzaderas ligeras en tuzik, quiero mencionar una de sus desventajas: ¡teme al fuego! En otras palabras, debe recordarse que la proximidad del fuego puede arruinar su barco; incluso el toque de un cigarrillo encendido derrite la espuma.
El dibujo teórico es la base del proyecto de cualquier barco, y no puedes prescindir de él cuando construyes un barco. Sin embargo, en papel, no es adecuado para trabajos de construcción: una pequeña escala conduce a errores al tomar mediciones y, lo más importante, no permite marcar los detalles del caso directamente.
Para la construcción del casco del barco, el dibujo teórico debe realizarse en tamaño completo. Tal dibujo se llama una disposición o un dibujo de borrador; se dibuja en un piso plano de madera o en grandes láminas de contrachapado: una plaza. Las desviaciones al realizar una plaza y quitarle plantillas no deben exceder de 1 a 2 mm. Para pasar de un dibujo teórico, hecho en el diseño a la escala, al de plasma, se compila una tabla de las ordenadas del piso. En esta tabla, las ordenadas se indican en tamaño completo, es decir, las dimensiones tomadas del dibujo teórico se multiplican por su escala. Las ordenadas se establecen para todas las líneas curvas de un dibujo teórico por marcos y agrupadas por proyecciones. El grupo de agua recibe las alturas desde la línea principal de la lengua (muesca en forma de cuña en la quilla y el tallo de las tablas de revestimiento que se adhieren a ellas), glúteos, cubiertas, pómulos, quilla; en el otro grupo - medias anchuras (desde el plano diametral, en adelante - DP) de las líneas de agua, líneas de pómulos y lados en la cubierta; ordenadas de los peces. Algunas dimensiones, como las dimensiones para la construcción de los contornos del vástago y las aletas, no se incluyen en la tabla de ordenadas de plasma, pero generalmente se indican en el dibujo teórico en sí.
Por supuesto, para usar la tabla de ordenadas, necesita saber a qué distancias se ubican uno a uno los planos de corte, es decir, la distancia entre los marcos es el espaciado, así como la distancia entre las líneas de agua y entre las nalgas.
Se sabe que la posición de cualquier punto en el espacio está determinada únicamente por tres coordenadas relativas a tres planos de base mutuamente perpendiculares. La tabla de ordenadas es un conjunto de coordenadas, que se utilizan para establecer la posición de un gran número de puntos que fijan la posición de la superficie del casco del barco en el espacio. Por lo tanto, en números, en una forma tabular muy conveniente, una forma de caja arbitrariamente compleja puede ser "programada". Para la construcción del barco, solo se necesita una proyección del dibujo teórico: el "Cuerpo" y los contornos del pivote. Las proyecciones de "Ancho medio" y "Lateral" se utilizan solo para líneas coincidentes.
Para ahorrar espacio en la plaza, puede dibujar las proyecciones "Side" y "Semirashire" una sobre otra. Bueno, si las líneas serán de diferentes colores. En la proyección del cuerpo, se deben dibujar las ramas de los lados derecho e izquierdo del marco. Es mejor combinar las costillas (por el color de las líneas) en los grupos de proa y popa (contando desde la sección media).
El uso de un dibujo teórico incorrectamente construido puede llevar a alteraciones. Con un desglose del diseño, el constructor puede dibujar cualquier parte del casco en tamaño completo. Hay pocos detalles de este tipo. Esto es principalmente la quilla, vástago, arbusto de popa, travesaño, knopa, tejidos de ideas y barras de madera. Todo esto constituye la pestaña del buque. El marcador debe su nombre al hecho de que cuando se ensambla forma, por así decirlo, la base de todo el conjunto: el esqueleto de la embarcación. La altura de la quilla generalmente se indica en el dibujo de construcción en varias secciones, el ancho se toma teniendo en cuenta el ancho medio de la lengüeta de la tabla de ordenadas de laicos. La sección transversal de la quilla, como cualquier otra conexión longitudinal, es fácil de construir directamente en la proyección de "Proyección" en cualquier marco teórico. Para calcular la lengüeta en el vástago, debe usar otra proyección: “Medio ancho”, en la que las secciones del vástago a lo largo de las líneas de agua se presentan en su forma verdadera.
Usando el marcado en la plaza, hacen plantillas para las cuales es fácil colocar los detalles del marcador en espacios en blanco de madera, y luego procesarlos en un "tamaño puro" que corresponde exactamente al dibujo teórico. Otros detalles de una forma compleja se dibujan en la plaza, por ejemplo, barras de cimentación para el motor (primero debe marcarse la posición del eje del eje), se especifica la posición de los eslabones longitudinales y se representan sus secciones transversales en los marcos (si es necesario, los recortes para el paso de los largueros se hacen en el conjunto transversal).
El constructor aficionado no siempre puede dibujar completamente un dibujo teórico de incluso un bote pequeño, ya que para ello es necesario tener un espacio libre bastante grande, herramientas apropiadas: listones largos flexibles - reglas, abrazaderas - ratas para fijar la posición de los rieles curvos, etc. d., y lo más importante - habilidades suficientes. Al tener una tabla de ordenadas, puede limitarse a desglosar solo una, la más necesaria y pequeña en proyección de área: "Estuche", colocándola en una hoja de papel grueso, que se puede doblar fácilmente en un rollo y quitar durante los descansos en el trabajo. Si en una plaza tan improvisada también dibuja un contorno del vástago y el ángulo de inclinación del travesaño, esto será suficiente para ensamblar el casco.
Pero uno puede prescindir de la ruptura de una sola proyección de "Caso" solo si los marcos prácticos se basan en el dibujo teórico que se incluye en el conjunto del casco del barco. Si los marcos del dibujo teórico no coinciden con los marcos prácticos, es necesario irrumpir en la plaza al menos una proyección más: “Media latitud”. Después de haber marcado la posición de los marcos prácticos en la proyección de “medio ancho” de acuerdo con el marco definido por el dibujo de diseño (el dibujo, que muestra todos los componentes y detalles de la construcción del casco con las dimensiones básicas), retire las ordenadas de la línea de flotación de estos marcos en los marcos y transfiéralos a la proyección “Vivienda” . Para resistir los contornos de la construcción del dibujo teórico (y solo entonces la calidad y el aspecto del barco coincidirán con los proyectados), es necesario conocer la regla sobre la posición de las líneas teóricas de los elementos estructurales del casco.
La línea teórica es la línea de la superficie del elemento estructural, que coincide con la línea del dibujo teórico. Tales líneas para un recipiente de madera con un tablón o forro de cremallera son:
línea externa de la piel; en la fabricación de marcos, muñones y quillas, el grosor de la piel debe depositarse hacia el interior a partir de las líneas teóricas de estos elementos;
la línea de la superficie interna del piso de la cubierta, en otras palabras, el borde superior de la viga, que coincide con la línea de la viga del dibujo teórico;
la línea del borde de popa de los marcos nasales y el borde nasal de los marcos de popa;
en la fabricación de marcos y mamparos por descomposición del plasma (menos el grosor de la piel) es necesario seguir estrictamente la regla de las líneas teóricas, y luego quitar las perlas (cortar la esquina) al instalar la piel no cambiará los contornos;
Línea de borde de carling y largueros, invertida por KDP.
Al dividir la plaza de madera contrachapada y de los botes de plástico, como regla general, no se debe tener en cuenta el grosor del revestimiento, es decir, los contornos de los marcos también son líneas teóricas (al desviarse de esta regla general, la tabla correspondiente debe indicarse en la tabla de ordenadas). Todas las líneas teóricas de los elementos estructurales están perforadas en un dibujo y las dimensiones y patrones necesarios ya están tomados de ellas. Para producir piezas exactamente de acuerdo con el dibujo de diseño no es todo. Es necesario colocarlos correctamente en su lugar, es decir, fijar cada detalle de modo que su posición con respecto a los tres planos de referencia: principal (en altura), diametral (en ancho) y medio marco (completo) - se corresponda estrictamente con el dibujo teórico y plazma . Por lo tanto, cuando se prepara para las piezas, la posición de las líneas de control se transfiere desde el plano de enchapado: DP, línea de flotación o cualquier otra línea paralela a ellas con la indicación de la distancia a ellas. Genuino, por ejemplo, la posición de la parte está completamente determinada por el número del cuadro; si esto no es suficiente, se indica la distancia al cuadro más cercano.
Bote plegable hecho en casa Matryoshka
El "barco de matryoshka" hecho de madera contrachapada por el diseño de L. Afrin consta de partes que se doblan una en la otra durante el transporte, como una muñeca-matryoshka (Fig. 1). Dicho barco es fácil y conveniente de transportar, puede ser transportado en autobús o en tren. Es muy fácil de fabricar y pesa solo 12-17 kg. La capacidad de carga es de 100-110 kg.
La figura 1. El diseño del barco a partir de dos secciones: 1 - revestimiento; 2,3,4 - detalles del barco; 5 - rastrillo
Para la fabricación de la embarcación se necesitarán:
dos láminas de madera contrachapada de 4 mm, tamaño 1525 x 1525 mm.
ancho tablero de pino espesor de 1.5-2 cm
listones delgados
Tira de estaño de 2-2,5 cm de ancho (se puede cortar con latas)
aceite de secado
pintura al óleo
Uñas de 50mm.
Primero, dos espacios en blanco de madera contrachapada 1 y espacios en blanco 2, 3 y 4 se cortan de madera contrachapada, después de haber sido tapizados con adornos de madera contrachapada en ambos lados. Recortar los espacios en blanco y las hojas de madera contrachapada en las juntas están recubiertas con una pintura al óleo espesa, pegamento "Phoenix", "Unikum" o pegamento epoxi.
Luego, la carcasa de madera contrachapada 1 se clava en las partes 2, 3 y 4. Para evitar que se astille en los bordes de la madera contrachapada, perfore previamente los orificios a lo largo de los bordes de la carcasa con una broca de Ø2 mm. Las partes de proa y popa ensambladas de la embarcación están conectadas de manera que la proa se encuentra en la popa por 3-4 cm. Todas las juntas están cubiertas con rayas de estaño y, antes de la tapicería, cubren la superficie con pintura al óleo gruesa. Después de eso, clava la quilla del riel en la parte inferior del bote y las lamas en los lados.
El bote terminado se trata por dentro y por fuera con aceite de linaza caliente, y después del secado, el recipiente se cubre con dos capas de pintura al óleo en ambos lados, sellando cuidadosamente todas las ranuras y ranuras. La proa de la embarcación está hecha de espuma de construcción densa, cuyas láminas están pegadas con pegamento epóxico o pintura al óleo sobre aceite de secado natural. Después de eso, la nariz de la embarcación se cubre con dos o tres capas de gasa, empapándolas con pegamento epóxico o pintura al óleo sobre aceite de secado natural. La nariz terminada se une a la placa de la nariz con dos pernos prisioneros. La parte de forraje también está hecha de espuma plástica.
Los remos del barco doble, como en un kayak. La longitud total de la paleta es de 220 a 240 cm. Puede usar paletas de madera o de kayak de madera ya preparadas, que están disponibles comercialmente.
Por lo general, los constructores de barcos aficionados, cuando se reúnen con cualquier material nuevo, lo evalúan principalmente desde el punto de vista de la aplicabilidad para construir un barco. Polyfoam no fue una excepción. Inmediatamente comenzó a utilizarse como aislamiento, para garantizar la inundabilidad, cuando se construyen recipientes de fibra de vidrio, para la fabricación de unidades de ensamblaje. Pero por alguna razón, la espuma no se usa como material estructural principal, aunque, en mi opinión, puede y debe estar hecho de ella.
Permítame recordarle las principales ventajas del plástico de espuma en comparación con los materiales "tradicionales" que se utilizan comúnmente para la construcción de este tipo de barcos (no hablaremos de termoplásticos que aún no están disponibles). Polyfoam es liviano, tiene suficiente resistencia, alta calidad de aislamiento térmico, está bien cortado y aserrado (las espumas como PS-1 y PSBS se cortan perfectamente con una cuerda de nicrom calentada mediante la conexión de corriente eléctrica), bien pegadas. Por otro lado, es imposible doblar la espuma.
Para probar las capacidades del PS-1 de grado de espuma, le hice un bote de remo no sumergible no seleccionable "Gamma", que, con un peso de aproximadamente 20 kg, tiene una capacidad de carga de 120 kg y es muy conveniente de operar, especialmente cuando se pesca en un automóvil.
En el diseño, la elección de la forma del casco resultó ser lo más difícil: era necesario hacer un pequeño bote de elementos planos, flexible, fácil de hacer y conveniente.
Al final, resultó que el bote estaba hecho de espuma con un mástil de popa y popa, parte delantera quillada, lados inclinados (con colapso) y un fondo plano, algo elevado a la popa (aquí se instala la aleta de popa).
zoom, 1248х2642, 326 KB
I - popa de popa; II - a popa del costado (2 piezas); III - parte de popa del fondo; IV - tablero (2 piezas); V - abajo; VI - la nariz de la cuenta (2 uds.); VII - lámina cigomática (2 piezas); VIII - popa nasal.
Las partes planas separadas con un grosor de 30 mm forman una estructura monolítica después del pegado. Los travesaños están hechos de una hoja dos veces más gruesa y suavemente inclinada a lo largo del contorno. Los bordes de unión de las partes a unir se cortan en ángulo, como se muestra en. Esto da un aumento en el área de pegado a lo largo de las uniones y simplifica de alguna manera el corte de las hojas, ya que no hay necesidad de volver a calcular las dimensiones para el grosor de la pieza de conexión.
La construcción del barco de espuma se puede dividir en tres etapas: láminas de corte - haciendo partes del cuerpo; piezas de montaje en las juntas - montaje; Unión y acabado final.
Para un uso más eficiente del material al cortar hojas, recomiendo cortar patrones de papel grueso. Después de cortar todas las partes a lo largo de los bordes que se unirán, el ángulo debe cortarse; el chaflán se debe cortar al valor n (vea el dibujo anterior), que se determina por la fórmula dependiendo del ángulo central a y el grosor de la hoja 6:
Si no confía en la rectitud de los bordes, solo uno de ellos debe cortarse "en ángulo"; El borde que lo une tendrá que ser personalizado durante el montaje.
Para la conveniencia de la instalación y el montaje, es mejor hacer una pila de cinco pares de bloques de quilla "transversales" y dos pares de "longitudinales", fijando la posición del fondo y los lados, así como el travesaño de proa y popa.
El pegado puede hacerse con cualquier pegamento recomendado para espuma de polietileno. Usé pegamento epoxi a base de resina ED-5. Después de que el pegamento se haya levantado completamente, afiló el borde libre del tablero y colocó una cuenta de madera alrededor del perímetro del casco, una tira de roble sobre el pegamento y los tornillos. Para mayor confiabilidad en todas las esquinas y juntas a tope en el nivel del borde superior del talón, afuera impuso unas tiras longitudinales hechas de aleación AMg (tira 1.5X20, 130 mm de largo, en el lado desde el eje de la junta). La aleta de forraje colocada en la parte inferior también estaba unida con la misma tira.
Después de la aplicación de masilla y pelado, la cubierta se recubrió con esmalte nitro en el exterior y el interior. Esta protección resultó ser prácticamente suficiente, por lo que es muy posible hacerlo sin pegar la espuma con fibra de vidrio, etc.
Los tarros extraíbles, que sirven simultáneamente como cruces, arqueando los lados, están hechos de madera en el Gamme. Serán más fáciles si se recortan de espuma plástica, al correr alrededor de los bordes de los listones de madera de refuerzo. Los bancos se cuelgan en los lados con la ayuda de clips - empuñaduras, dobladas de trozos de aleación AMg. El volante se cuelga de los pasadores y se fija en el espejo de popa.
Habiendo comenzado ya a probar el Gamma, todavía dudaba de la exactitud de la elección del material, temiendo por la resistencia del cuerpo de espuma. Sin embargo, con cada nueva salida gané más y más confianza en mi barco. Nadar en una variedad de condiciones, transportar y arrastrar con resistencia, cuando es difícil excluir todo tipo de golpes, a veces muy fuerte, mostró que el barco es fuerte (incluso cuando no está arreglado por bancos) y confiable. Y no hay nada que decir sobre la capacidad de inundación: es casi imposible ahogar a Gamma. El barco de espuma tiene otras ventajas específicas. La falta completa de reclutamiento y cualquier lodo ayuda a mantener limpio el interior del barco. Debido a las buenas cualidades de aislamiento térmico de la espuma en el barco, puede sentarse directamente en la parte inferior; cuando la sacan a tierra, me quedo allí para pasar la noche sin arriesgarme a resfriarme del suelo.
Cuando recomiendo el poliestireno para hacer lanzaderas ligeras en tuzik, quiero mencionar una de sus desventajas: ¡teme al fuego! En otras palabras, debe recordarse que la proximidad del fuego puede arruinar su barco; incluso el toque de un cigarrillo encendido derrite la espuma.
Por lo general, los constructores de barcos aficionados, cuando se reúnen con cualquier material nuevo, lo evalúan principalmente desde el punto de vista de la aplicabilidad para construir un barco. Polyfoam no fue una excepción. Inmediatamente comenzó a utilizarse como aislamiento, para garantizar la inundabilidad, cuando se construyen recipientes de fibra de vidrio, para la fabricación de unidades de ensamblaje. Pero por alguna razón, la espuma no se utiliza como material estructural principal, aunque, en mi opinión, los botes pequeños, lanzaderas y remolcadores, pueden y deben estar hechos de ella.
Permítame recordarle las principales ventajas del plástico de espuma en comparación con los materiales "tradicionales" que se utilizan comúnmente para la construcción de este tipo de barcos (no hablaremos de termoplásticos que aún no están disponibles). Polyfoam es liviano, tiene suficiente resistencia, alta calidad de aislamiento térmico, está bien cortado y aserrado (las espumas como PS-1 y PSBS se cortan perfectamente con una cuerda de nicrom calentada mediante la conexión de corriente eléctrica), bien pegadas. Por otro lado, es imposible doblar la espuma.
Para probar las capacidades del PS-1 de grado de espuma, le hice un bote de remo no sumergible no seleccionable "Gamma", que, con un peso de aproximadamente 20 kg, tiene una capacidad de carga de 120 kg y es muy conveniente de operar, especialmente cuando se pesca en un automóvil.
Dimensiones principales del barco de espuma.
Longitud máxima, m 2.60
Anchura según ancho de vía, m 1.05
Ancho de fondo, m 0.78
Altura del barco midship, m 0.38
Altura de la tabla en las extremidades, m 0.40
En el diseño, la elección de la forma del casco resultó ser lo más difícil: era necesario hacer un pequeño bote de elementos planos, flexible, fácil de hacer y conveniente.
Al final, resultó que el bote estaba hecho de espuma con un mástil de popa y popa, parte delantera quillada, lados inclinados (con colapso) y un fondo plano, algo elevado a la popa (aquí se instala la aleta de popa).
Dibujo teórico del casco de la embarcación de espuma.
Piezas de corte de espuma para embarcaciones
I - popa de popa; II - a popa del costado (2 piezas); III - parte de popa del fondo; IV - tablero (2 piezas); V - abajo; VI - la nariz de la cuenta (2 uds.); VII - lámina cigomática (2 piezas); VIII - popa nasal.
Las partes planas separadas con un grosor de 30 mm forman una estructura monolítica después del pegado. Los travesaños están hechos de una hoja dos veces más gruesa y suavemente inclinada a lo largo del contorno. Los bordes de unión de las partes a unir se cortan en ángulo, como se muestra en el boceto de la embarcación. Esto da un aumento en el área de pegado a lo largo de las uniones y simplifica de alguna manera el corte de las hojas, ya que no hay necesidad de volver a calcular las dimensiones para el grosor de la pieza de conexión.
La construcción de un bote de espuma se puede dividir en tres etapas: láminas de corte: fabricación de piezas de casco; piezas de montaje en las juntas - montaje; Unión y acabado final.
Diagrama de la conexión angular de piezas.
Para un uso más eficiente del material al cortar hojas, recomiendo cortar patrones de papel grueso. Después de cortar todas las partes a lo largo de los bordes que se unirán, el ángulo debe cortarse; el chaflán se debe cortar al valor n (vea el dibujo anterior), que se determina por la fórmula dependiendo del ángulo central a y el grosor de la hoja 6:
Si no confía en la rectitud de los bordes, solo uno de ellos debe cortarse "en ángulo"; El borde que lo une tendrá que ser personalizado durante el montaje.
Para la conveniencia de la instalación y el montaje, es mejor hacer una pila de cinco pares de bloques de quilla "transversales" y dos pares de "longitudinales", fijando la posición del fondo y los lados, así como el travesaño de proa y popa.
Cuerpo pegado en las existencias.
El pegado puede hacerse con cualquier pegamento recomendado para espuma de polietileno. Usé pegamento epoxi a base de resina ED-5. Después de que el pegamento se haya levantado completamente, afiló el borde libre del tablero y colocó una cuenta de madera alrededor del perímetro del casco, una tira de roble sobre el pegamento y los tornillos. Para mayor confiabilidad en todas las esquinas y juntas a tope en el nivel del borde superior del talón, afuera impuso unas tiras longitudinales hechas de aleación AMg (tira 1.5X20, 130 mm de largo, en el lado desde el eje de la junta). La aleta de forraje colocada en la parte inferior también estaba unida con la misma tira.
Después de la aplicación de masilla y pelado, la cubierta se recubrió con esmalte nitro en el exterior y el interior. Esta protección resultó ser prácticamente suficiente, por lo que es muy posible hacerlo sin pegar la espuma con fibra de vidrio, etc.
Los tarros extraíbles, que sirven simultáneamente como cruces, arqueando los lados, están hechos de madera en el Gamme. Serán más fáciles si se recortan de espuma plástica, al correr alrededor de los bordes de los listones de madera de refuerzo. Los bancos se cuelgan en los lados con la ayuda de clips - empuñaduras, dobladas de trozos de aleación AMg. El volante se cuelga de los pasadores y se fija en el espejo de popa.
Habiendo comenzado ya a probar el Gamma, todavía dudaba de la exactitud de la elección del material, temiendo por la resistencia del cuerpo de espuma. Sin embargo, con cada nueva salida gané más y más confianza en mi barco. Nadar en una variedad de condiciones, transportar y arrastrar con resistencia, cuando es difícil excluir todo tipo de golpes, a veces muy fuerte, mostró que el barco es fuerte (incluso cuando no está arreglado por bancos) y confiable. Y no hay nada que decir sobre la capacidad de inundación: es casi imposible ahogar a Gamma. El barco de espuma tiene otras ventajas específicas. La falta completa de reclutamiento y cualquier lodo ayuda a mantener limpio el interior del barco. Debido a las buenas cualidades de aislamiento térmico de la espuma en el barco, puede sentarse directamente en la parte inferior; cuando la sacan a tierra, me quedo allí para pasar la noche sin arriesgarme a resfriarme del suelo.
Cuando recomiendo el poliestireno para hacer lanzaderas ligeras en tuzik, quiero mencionar una de sus desventajas: ¡teme al fuego! En otras palabras, debe recordarse que la proximidad del fuego puede arruinar su barco; incluso el toque de un cigarrillo encendido derrite la espuma.
Este bote de espuma hecho en casa "atrapó" peces que van desde el pueblo de Rogozhkino en el Bajo Don hasta el Río Seco bajo el embalse de Tsimlyansk; Viajó casi todo el río Manych y se encontraba en el embalse Veselovsky; visitó el río Tuzlov y el Gorsky poco profundo del río Don, etc.
El bote es pequeño y muy ligero, fácil de levantar y transportado por una sola persona. El aspecto del barco no es impresionante, pero cuando estaba pescando, los pescadores me preguntaron muchas veces cómo se hizo.
Todo comenzó con el deseo de tener el barco más fácil de transportar en automóvil.
Volví a leer un montón de revistas "Barcos y yates" y decidí hacer un bote de acuerdo con las recomendaciones tradicionales construyendo un casco de tablero de fibra, seguido de pegar fibra de vidrio en resina epoxi.
La etapa de corte de piezas brutas de tablero de fibra fue bien, la unión con el cable fue peor, ya que toda la estructura se arrastró sin mantener la forma deseada.
Después de un uso del ingenio natural, el futuro bote mostró bellamente el fondo del cielo.
Es hora de pegar la fibra de vidrio.
Después de varios intentos, la notable construcción fue destruida con una velocidad sin precedentes.
Para pegar la fibra de vidrio con resina epoxi, es necesario tener habilidades que no tenía, así como los pensamientos de ganar dinero haciendo barcos.
En el momento de la destrucción del futuro barco, una idea muy simple nació en mi cabeza, que se encarnó rápidamente en una forma material.
El contenido fue movido de la página "Botes caseros para pescar" muerto a muerte
Se espera una edición seria.
Hoy es mayo 2016
Cómo hacer un bote de espuma con tus propias manos.
Se compró espuma en lámina y, solo disponible para la venta, espuma de construcción.
La espuma se cortó en trozos, se torció con tornillos y se pegó con espuma.
El resultado es genial.
Bote de espuma
- absolutamente insumergible,
- pesa muy poco
- luz sobre remos.
El barco no es muy bonito :), pero lo principal no es la belleza sino el efecto práctico.
Es probable que esta historia empuje el pensamiento de alguien en la dirección correcta.
El barco ha estado inactivo durante mucho tiempo en el patio. Es probable que sea más útil.
- La longitud del barco es de 260 cm.
- Altura del tablero 34 cm.
- Ancho 100 cm.
- Espesor de la espuma: tablero de 50 mm. fondo 70 mm.
En la popa y en la proa se atornillaron con tornillos de tablero. Están podridos con la vejez.
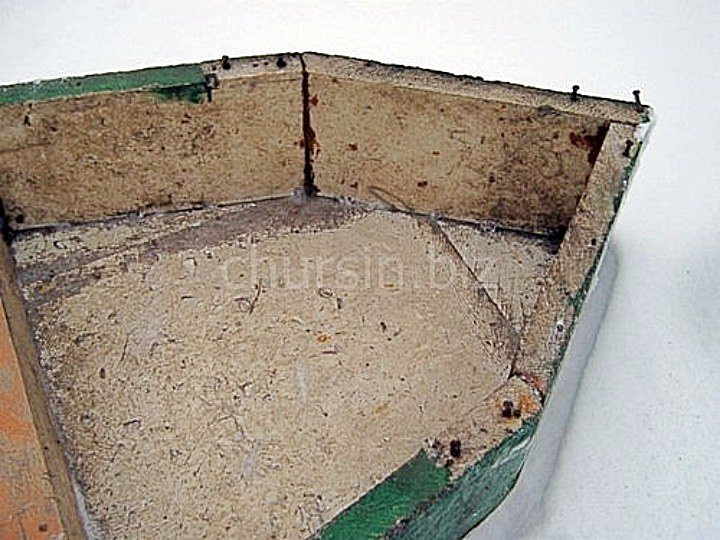

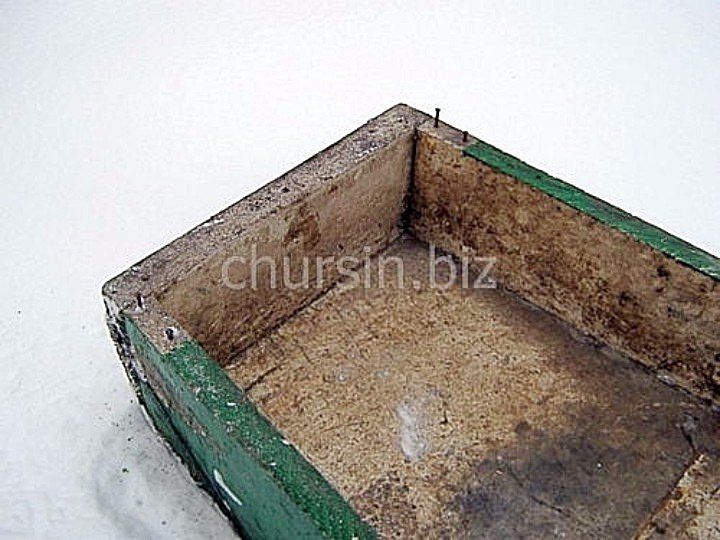